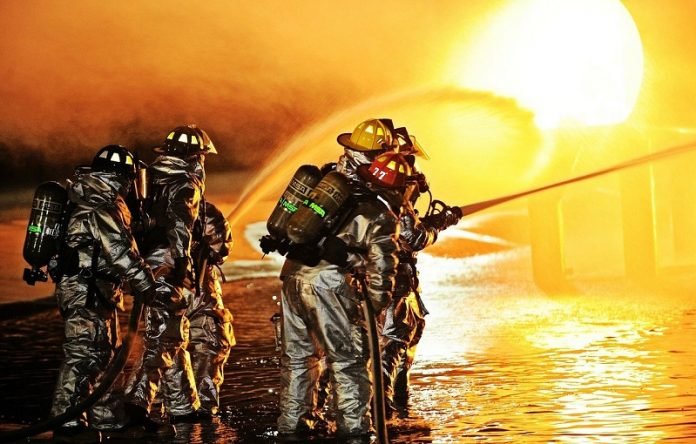
Firefighters risk their lives battling blazes, and aging protective gear can put them at even greater risk.
A University of Alberta researcher is working with industry to reduce that risk with a sensor that can detect the gradual breakdown in garments from exposure to heat, moisture and ultraviolet (UV) light.
“These fibers age silently and lose their performance, so this sensor technology is a breakthrough in terms of safety for workers exposed to heat and flame,” said clothing and textiles scientist Patricia Dolez, the project’s lead researcher and an assistant professor in the U of A Faculty of Agricultural, Life & Environmental Sciences (ALES).
Damage to the garments may not be visible to the naked eye before performance is reduced considerably, said Dolez, a researcher in the Department of Human Ecology.
“Firefighters have no good way to know how safe their clothing really is—you can’t tell just by looking at it.”
Once fully developed, the sensor patch would provide a way to assess the garment without destructive testing—for example, having to cut out samples to test the fabric’s condition through conventional methods such as strength testing.
Developed in partnership with Edmonton-based company Davey Textile Solutions and other industry partners, the sensor patch uses graphene, a flaky substance composed of carbon atoms, to form conductive tracks on the patch’s surface.
When exposure to heat, moisture or UV light exceeds a certain level, the graphene track is disrupted and loses its electrical conductivity.
Firefighters would use a simple voltmeter to check the safety levels of their clothing on the sensor patch—a result that comes within seconds.
The sensor has been provisionally patented and is still under development.
It comes at an optimal time, Dolez said, as the National Fire Protection Association (NFPA) prepares to upgrade its recommendations on garment maintenance because of an underlying threat of diseases such as cancer, which can be caused by fire-associated harmful substances leaching into the fabric.
“The current recommendation is to wash firefighting garments twice a year, but the problem is all the existing data that determines when the clothing needs to be replaced is based on that once- or twice-a-year washing,” she said.
New NFPA recommendations are expected to bump up the laundering frequency to after each exposure to a firefighting incident, which means the monitoring technology also needs to be amped up.
“The sensor is important to be able to gauge what the garment is going through with each washing.”
Davey Textile Solutions, one of five industry partners working with Dolez, manufactured the fire-resistant fabrics that will be used as part of the sensor patch.
The company is producing reflective trims for protective garments.
The sensor could also be used in the oil and gas, electrical, construction and mining industries, said Lelia Lawson, research and development specialist for Davey Textile Solutions.
“This is an example of how we try to be ahead of the curve to provide new proactive items to the marketplace,” said Lawson, noting that one of the biggest questions for clients in heavy industry is knowing when to retire personal protective equipment (PPE).
“The sensor takes the ambiguity out of that question.”
The sensor research, which began in 2018, also includes the expertise of Jane Batcheller from the U of A Department of Human Ecology and Hyun-Joong Chung, associate professor in the Department of Chemical and Materials Engineering.
The work has produced two scientific papers by graduate students studying clothing and textiles science in ALES and chemical and materials engineering in the Faculty of Engineering.
The papers explored the application of graphene on high-performance fabrics and how its conductivity is affected by different aging conditions simulating service use.
Through the Human Ecology Practicum Program, a student worked with Davey Textiles Solutions to develop a business case for market applications for the sensor. The student “was able to provide a lot of good information which supported the need for this product in the industry,” Lawson said.
The expertise offered by the company is invaluable, said Dolez.
“Their collaboration ensures that what we develop will be relevant for industry. As researchers we can develop something that is a great idea, but if no one is able to produce it, it’s not useful,” she said.
“By having industries like Davey Textile Solutions at the table, we’re making sure what we develop will end up being used.”
The sensor technology is the latest in a series of projects the Department of Human Ecology has had with the company through the U of A’s Protective Clothing and Equipment Research Facility, including developing clothing to protect workers against steam burns.
That work resulted in the Canadian General Standards Board updating a standard used by employers when selecting appropriate PPE for their workers.
Currently, Dolez and Davey Textile Solutions are collaborating to develop methods to recycle cotton-based material from used industrial coveralls—otherwise destined for the landfill—into fibers that can be used to make new textiles.
“We’re aiming to manufacture new fabrics for PPE and for other consumer goods,” Lawson said. “There are more clients who want to purchase sustainable products.”
Working with various U of A researchers from human ecology and the Department of Mechanical Engineering, Davey Textiles Solutions benefits greatly from their applied research, Lawson said.
“We can commercialize products from their work, and it’s rewarding to have research that evolves into something that can be realized in the marketplace.”
The company has hosted practicum students over the years who bring fresh perspectives to developing clothing and textiles, Lawson said, adding that the company has hired six graduates from the human ecology program, including her.
“It speaks volumes to the caliber of students from the program. They are very well-rounded because they study humans in their near environment, how they interact.
Along with the theoretical knowledge of textiles, they also help with understanding how these textiles can impact lives. And that helps create better products.”
Written by Bev Betkowski.