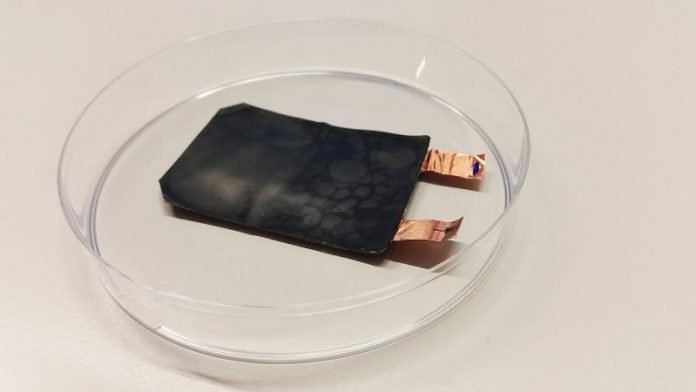
A new bendable battery can stretch and twist without interrupting the supply of power.
For applications in bendable electronic devices, this is precisely the kind of battery they need.
Today’s electronics industry is increasingly focusing on computers or smartphones with screens that can be folded or rolled.
Smart clothing items make use of wearable micro-devices or sensors to monitor bodily functions, for example.
All these devices need an energy source, however, which is usually a lithium-ion battery.
Unfortunately, commercial batteries are typically heavy and rigid, making it fundamentally unsuitable for applications in flexible electronics or textiles.
What makes this new battery prototype special is its electrolyte—that part of the battery through which lithium-ions move when the battery is charged or discharged. Lead author Xi Chen, a doctoral student at ETH Zurich, discovered the electrolyte.
Following the design of commercial batteries, this new type of battery is built in layers like a sandwich. However, it marks the first time that researchers have used flexible components to keep the whole battery bendable and stretchable.
“To date, no one has employed exclusively flexible components as systematically as we have in creating a lithium-ion battery,” says Markus Niederberger, professor for multifunctional materials, whose team developed the battery prototype.
The two current collectors for the anode and the cathode consist of a bendable polymer composite that contains electrically conductive carbon and that also serves as the outer shell.
On the interior surface of the composite, the researchers applied a thin layer of micron-sized silver flakes.
Due to the way the flakes overlap like roof tiles, they don’t lose contact with one another when the elastomer is stretched. This guarantees the conductivity of the current collector even if it is subjected to extensive stretching.
And in the event that the silver flakes do in fact lose contact with each other, the electrical current can still flow through the carbon-containing composite, albeit more weakly.
With the help of a mask, the researchers then sprayed anode and cathode powder onto a precisely defined area of the silver layer. The cathode is composed of lithium manganese oxide and the anode is a vanadium oxide.
In the final step, the scientists stacked the two current collectors with the applied electrodes on top of each other, separated by a barrier layer similar to a picture frame, while they filled the gap in the frame with the electrolyte gel.
Niederberger emphasizes that this gel is more environmentally friendly than the commercial electrolytes: “Liquid electrolyte in today’s batteries are flammable and toxic.”
In contrast, the gel electrolyte that Chen developed contains water with a high concentration of a lithium salt, which not only facilitates the flow of lithium ions between cathode and anode while the battery is charging or discharging but also keeps the water from electrochemical decomposition.
The scientists joined the various parts of their prototype together with adhesive. “If we want to market the battery commercially, we’ll have to find another process that will keep it sealed tight for a longer period of time,” Niederberger says.
More and more applications for a battery like this are emerging every day, the researchers say. Well-known manufacturers of mobile phones are vying with each other to produce devices with foldable screens.
Other possibilities include rollable displays for computers, smartwatches, and tablets, or functional textiles that contain bendable electronics—and all of these require a flexible power supply.
“For instance, you could sew our battery right into the clothing,” Niederberger says.
It’s important to ensure that, in the event of battery leakage, the liquids that come out cause no damage. This is where the team’s electrolyte offers a considerable advantage.
Niederberger stresses that more research is necessary to optimize the flexible battery before they consider commercializing it. Above all, the team has to increase the amount of electrode material it can hold.
The study appears in Advanced Materials.
Written by Peter Rüegg.