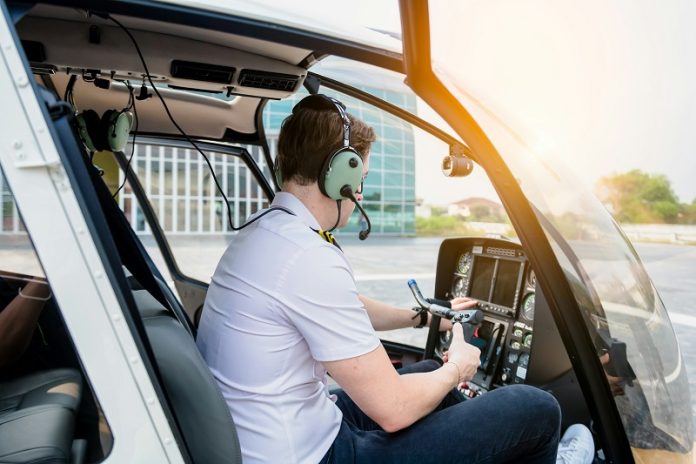
Helicopters draw a lot of attention with their almost magical ability to hover, fly in any direction and operate without runways.
They also help save many lives, often dramatically, with their extensive use in all-weather military missions, ambulance duties and search-and-rescue roles.
When things go wrong, dramatic images and news stories about helicopter accidents grab the public’s attention. This is especially true when high-profile celebrities or government officials are involved.
However, modern rotorcraft are safe. Each year, the U.S. commercial helicopter industry flies about 3 million flight hours. There were 0.77 fatal accidents per 100,000 flight hours on average from 2018 to 2022.
In comparison, general aviation, which refers to small fixed-wing aircraft and not jetliners, averaged 0.88 fatal accidents per 100,000 flight hours over the same period.
As an aeronautical engineer who specializes in rotorcraft and the director of a national vertical lift center of excellence, I have observed academic, government and industry efforts to improve helicopter safety.
A lot of technology and training have gone into making helicopters safe.
Long road to safety
Rotary-wing aircraft were first developed over a century ago. The first that went into mass production was the autogiro, developed in 1923 by Juan de la Cierva in Spain.
The pinwheel-like nature of the main lifting rotor avoided the dangers of stalling, which wrecked so many fixed-wing aircraft during that era. Stalling is when the angle of an airplane’s wings relative to the airflow is too great, causing the plane to lose lift.
Within 15 years, the first true helicopters with powered rotors—capable of hovering, low-speed flight and safe descent in the event of engine failure—were in the air in both Europe and the United States. Large-scale military and commercial production began just a few years later during the World War II.
Today’s helicopter operations are anchored on three main principles: comprehensive vehicle design, testing and manufacturing; well-trained flight crews; and thorough maintenance practices. Advanced technology plays a vital role in each of these pillars of helicopter safety.
Safety fundamentals
Helicopter safety begins with the fundamental capability of large-diameter rotors that can auto-rotate in the event of engine failure. With the engine off, the rotors spin freely, slowing the helicopter’s decent and allowing parachute-like controlled landing. Reliable powertrains—engines, gear boxes and driveshafts—long-lived blades and low-vibration airframes have also paved the way for safer flights.
Additionally, advanced autopilot and computer-controlled or assisted flight controls, terrain-avoidance radar and rotor blade deicing systems that enable all-weather flight have become common on modern helicopters.
Decades of basic and applied research conducted in university, government and industry laboratories has yielded many advanced technologies.
Today’s helicopters typically have radar- and lidar-based collision avoidance systems, comprehensive digital terrain mapping databases and adaptive controls that help the pilot feel differences depending on flight conditions and aircraft characteristics such as payload.
Rotorcraft do require specialized pilot training to master. Pilots often train on fixed-wing aircraft before transitioning to rotary-wing vehicles, much as you might learn to ride a bicycle before taking on a unicycle. Pilots spend many additional hours or even years of flight instruction to earn a helicopter license.
Rotorcraft inherently feature more moving parts than fixed-wing aircraft, which makes careful design of bearings, gearboxes, shock absorbers, lubrication systems and other mechanical components critical. As with pilots, helicopter mechanics need additional training hours and skill sets.
Indeed, for some complex military and rescue missions, mechanics fly along as integral members of the flight crew. These flight mechanics closely monitor critical systems using onboard temperature, vibration, noise and metal chip sensors, and can even troubleshoot and repair many mechanical, electrical and digital issues that arise.
Advanced sensors and computer software make maintaining helicopters quicker and more thorough. Additionally, advanced design and manufacturing methods for rugged composite materials and specialized flexible polymers have dramatically improved the durability of dynamic components such as blades and rotors.
Risks remain
Even with all the advanced design, training and technology in place, accidents happen. The vast majority involve a complex chain of events. Pilot ormechanic error, typically associated with unusual circumstances, is a primary cause of many crashes.
Bad weather often contributes. Many essential flight operations such as search and rescue, firefighting and military transport necessarily occur in sandy, snowy, smoky or stormy environments.
These “edge of the envelope” conditions raise the risk factor, despite the best technology and training doctrines. Even the intense and realistic training exercises for these missions can be inherently more dangerous than standard flight.
Advanced technologies
New technologies continue to improve flight safety under these difficult conditions.
These include more effective, reliable and lower power rotor blade deicing or anti-icing systems; improved weather forecasting models; and even onboard ice-cloud detection systems. Researchers are developing artificial intelligence-enabled expert systems that help pilots decide when and if it’s safe to fly.
I expect advanced technologies to enable reliability and safety statistics to continue to improve, and operating costs to drop, as thousands of aerospace engineers around the world bring life-saving, time-saving and security-enhancing improvements to these remarkable vehicles.
Written by Edward C. Smith, The Conversation.