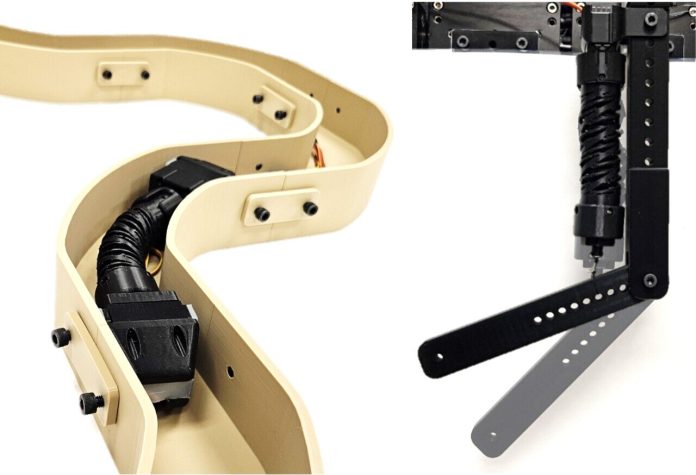
Engineers at Northwestern University have developed a new, low-cost device that makes robots move in a way similar to human muscles.
This device, called an actuator, allows for the creation of soft, flexible robots.
These new robots can be much safer and more practical for everyday use because they are less likely to cause injury if they accidentally hit someone.
To show how their new actuator works, the researchers built a worm-like robot and an artificial bicep.
The worm-like robot successfully navigated through a narrow, winding pipe, and the artificial bicep was able to lift a 500-gram weight 5,000 times in a row without breaking.
The best part is that these soft actuators were made using a common rubber and 3D printing, costing only about $3 for the materials, not including the small motor that powers them. This is a huge cost reduction compared to traditional actuators, which can be very expensive.
The study, led by Ryan Truby at Northwestern’s McCormick School of Engineering and his team, was published in the journal Advanced Intelligent Systems.
Truby, along with his postdoctoral scholar Taekyoung Kim and Ph.D. student Pranav Kaarthik, aim to make robots safer and more adaptable for human environments.
Traditional robot actuators are usually stiff and rigid, making them potentially dangerous if they come into contact with humans. In contrast, soft actuators are inspired by human muscles, which can contract and stiffen to perform tasks. Truby and his team wanted to create a material that could mimic this muscle behavior to make robots that move more like living organisms.
The team 3D-printed cylindrical structures called “handed shearing auxetics” (HSAs) out of rubber. HSAs have a complex design that allows them to expand and contract when twisted. Previous versions of these structures were made with expensive materials and printers, resulting in rigid and less flexible actuators. By using a common rubber called thermoplastic polyurethane, often found in cellphone cases, the team was able to make HSAs that were both soft and durable using a cheaper 3D printer.
However, the researchers faced a challenge: how to get a single motor to twist and activate a single HSA. To solve this, they added a soft, extendable rubber bellows to the structure, which acted like a rotating shaft. This allowed the motor to twist the HSA, causing it to extend and contract, similar to a muscle.
This innovation enabled the creation of a crawling robot that could move through a pipe-like environment using just one actuator. The pushing and pulling motions of the actuator propelled the robot forward. The new actuator also allowed the robots to become stiffer as they extended, much like human muscles do when they exert force.
The researchers believe this new actuator design is a significant step toward more bio-inspired robots. “Robots that can move like living organisms will enable us to think about robots performing tasks that conventional robots can’t do,” said Truby.
This development opens up new possibilities for soft robots in various applications, making them safer and more versatile for real-world use.
Source: Northwestern University