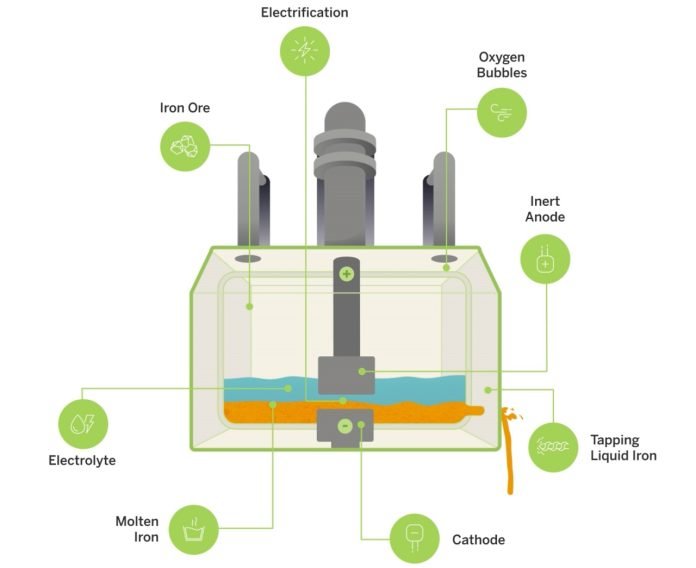
Steel is one of the most important materials in modern life, used in everything from buildings and cars to bridges and airplanes.
However, traditional steelmaking is a highly polluting process, contributing 7 to 9 percent of global greenhouse gas emissions.
Fortunately, a company called Boston Metal is aiming to clean up the steel industry using a new electrochemical process called molten oxide electrolysis (MOE).
Boston Metal’s innovative method, founded by MIT Professor Emeritus Donald Sadoway, Professor Antoine Allanore, and James Yurko PhD ’01, replaces the traditional dirty processes with one that uses electricity to produce steel.
This process not only simplifies steel production but also releases oxygen as its only byproduct.
The company is already using MOE to recover valuable metals from mining waste at its subsidiary in Brazil, Boston Metal do Brasil.
This work is helping the company scale up its technology for commercial use and form important partnerships with mining operators.
At its headquarters in Woburn, Massachusetts, Boston Metal has also built a prototype MOE reactor to produce green steel.
Boston Metal’s global ambitions are backed by more than $370 million in funding from organizations across Europe, Asia, the Americas, and the Middle East. The company aims to rapidly scale up and transform steel production worldwide.
“There’s a worldwide recognition that we need to act rapidly, and that’s going to happen through technology solutions like this,” says Boston Metal Chief Scientist Guillaume Lambotte.
Since the 1980s, Sadoway had been researching electrochemical processes, focusing initially on aluminum production.
He later began to explore a similar process for producing iron, the main ingredient in steel. In 2012, Sadoway and Allanore discovered an iron-chromium alloy that could serve as a cost-effective anode material, making the process commercially viable and producing oxygen as a byproduct.
They then partnered with James Yurko to found Boston Metal.
Lambotte joined the company after Sadoway’s team published a paper in 2013 detailing the MOE platform.
The technology quickly evolved from lab experiments to a company capable of producing large quantities of metal.
Boston Metal’s process takes place in modular MOE cells, each the size of a school bus.
Iron ore is fed into the cell, which contains a cathode and an anode immersed in a liquid electrolyte.
When electricity flows between the anode and cathode at around 1,600 degrees Celsius, the iron oxide bonds in the ore are split, producing pure liquid metal and oxygen.
This process doesn’t require water, hazardous chemicals, or precious-metal catalysts.
Each MOE cell can produce up to 10 tons of metal daily, depending on the size of the current. Steelmakers can license Boston Metal’s technology and deploy as many cells as needed to meet their production goals.
The company is already helping mining companies recover valuable metals from waste and plans to expand its technology to produce other metals, including chromium, which is essential for clean energy applications.
Boston Metal’s steel decarbonization technology is expected to reach commercial scale by 2026, but its Brazilian plant is already showcasing the benefits of MOE.
This plant operates entirely on renewable energy, demonstrating the potential for green steel production.
“Fully green steel requires green electricity,” Lambotte says. “Our approach goes hand in hand with the global push to decarbonize the energy sector.”
The company’s primary focus is on reducing the massive carbon footprint of the steel industry.
“Steel produces around 10 percent of global emissions, so that is our north star,” Lambotte says. With many industries pledging to reduce emissions and achieve net-zero goals, the steel industry is actively seeking viable solutions.
Boston Metal’s MOE technology offers a promising new approach to making steel that could significantly cut global emissions and pave the way for a more sustainable future.
Source: MIT.