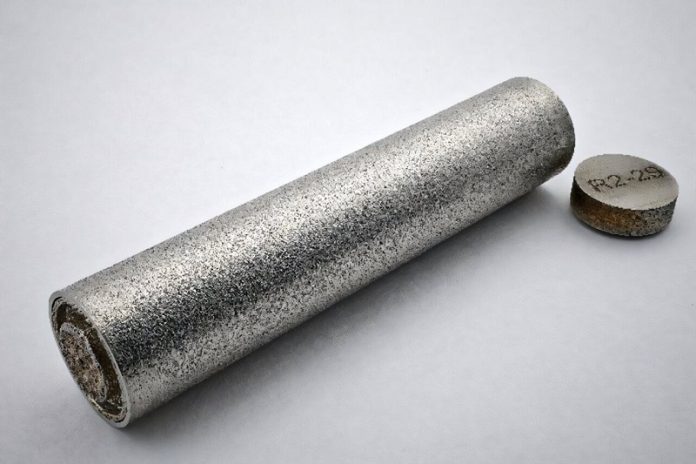
Scientists at Oak Ridge National Laboratory (ORNL) have achieved a major breakthrough by successfully testing two 3D-printed stainless steel capsules inside a nuclear reactor.
This marks a big step toward using 3D printing—also known as additive manufacturing—for making safe and reliable components in the nuclear industry.
The experiment took place at ORNL’s High Flux Isotope Reactor (HFIR), one of the world’s most powerful research reactors.
The capsules, made from a special type of stainless steel called 316H, were created using a laser-based 3D printing process at the lab’s Manufacturing Demonstration Facility.
This steel was chosen because it can handle high temperatures, resist corrosion and radiation, and is already trusted for nuclear applications.
These steel capsules play a crucial role in nuclear research. They are designed to safely hold samples during irradiation experiments, helping researchers understand how different materials behave under the extreme conditions inside a reactor.
The capsule itself serves as a protective barrier—keeping both the experiment and the reactor safe.
Once the capsules were printed and assembled, they were inserted into the reactor by ORNL’s Irradiation Engineering group. After spending a full month inside the reactor’s intense neutron environment, the capsules were removed without any damage. This success shows that 3D-printed parts can stand up to the tough conditions of a nuclear reactor.
According to Ryan Dehoff, director of the Manufacturing Demonstration Facility, this achievement could change how nuclear components are made in the future. If 3D printing becomes a standard manufacturing method, it could speed up production, cut costs, and make it easier to create custom parts for reactors.
Currently, designing and producing these capsules using traditional methods takes a lot of time and money. Additive manufacturing could simplify the process, helping researchers test new materials and fuels faster and more efficiently.
Richard Howard, a nuclear energy expert at ORNL, emphasized that the nuclear industry is under pressure to develop new reactor technologies that can survive extreme conditions. 3D printing gives researchers new tools to meet this challenge and push the boundaries of nuclear science.
This project was supported by the U.S. Department of Energy’s Office of Nuclear Energy through its Advanced Materials and Manufacturing Technologies program. The work also reflects broader goals of the DOE’s Office of Science, which funds research to solve some of today’s most urgent scientific and engineering problems.
In the future, the success of these 3D-printed capsules may lead to more printed components being used in nuclear reactors—making the technology safer, more affordable, and more adaptable than ever before.
Source: ORNL.