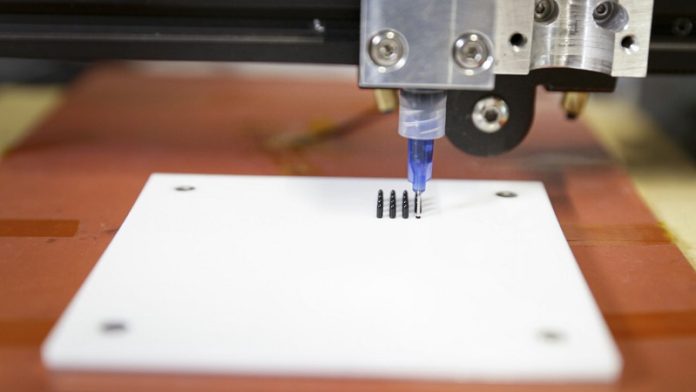
Researchers have found a way to 3D print powerful and sustainable thermoelectric materials, which could improve cooling technology in electronics, medicine, and energy harvesting.
This new method, developed by scientists at the Institute of Science and Technology Austria (ISTA), makes production cheaper, reduces material waste, and could lead to real-world applications.
Thermoelectric materials can generate electricity from temperature differences or create cooling effects when powered by electricity.
They are used in solid-state refrigerators and cooling systems for electronics, medical treatments, and more.
However, making these materials has traditionally been expensive and inefficient, requiring cutting large blocks of material (ingots) and producing a lot of waste.
To solve this problem, a team led by Professor Maria Ibáñez at ISTA, with postdoctoral researcher Shengduo Xu as the lead author, used 3D printing to create thermoelectric materials with high performance.
Unlike previous attempts, their method produces materials that work as well as traditional ones but at a lower cost.
“By integrating 3D printing into the process, we’ve significantly improved efficiency and reduced costs,” Xu explains. “Our materials perform at commercial levels, meaning they could be used beyond research and in real-world applications.”
Not all materials can efficiently convert heat into electricity or create cooling effects. The best thermoelectric materials are “doped semiconductors,” meaning they contain added elements to improve conductivity. Until now, manufacturers have relied on expensive and energy-intensive methods to make them.
By using 3D printing, the ISTA team can create these materials in the exact shape needed, eliminating waste. Their 3D-printed devices can achieve a cooling effect of up to 50 degrees Celsius, matching the performance of expensive, traditionally made materials.
One of the biggest challenges of 3D printing thermoelectric materials is ensuring the tiny particles bond together properly. The ISTA researchers developed special inks that, as they dry, form strong atomic bonds between particles. This improves charge transfer, making the material more efficient at converting energy.
“We designed our ink so that as the solvent evaporates, it creates a highly connected atomic network. This innovation enhances the performance of our 3D-printed materials and offers new insights into porous materials,” Ibáñez explains.
Beyond electronics, thermoelectric materials could be used in medical treatments such as burn care and muscle pain relief. They can also be adapted for energy harvesting, generating electricity from waste heat in industrial settings. This breakthrough could make thermoelectric technology more sustainable and widely available.
“Our work is a big step forward in producing efficient and eco-friendly thermoelectric devices,” says Xu. “This new method opens doors for sustainable technology in multiple industries.”
With this innovative approach, 3D printing could lead to the next generation of cooling and energy-efficient devices, transforming industries while reducing waste and costs.