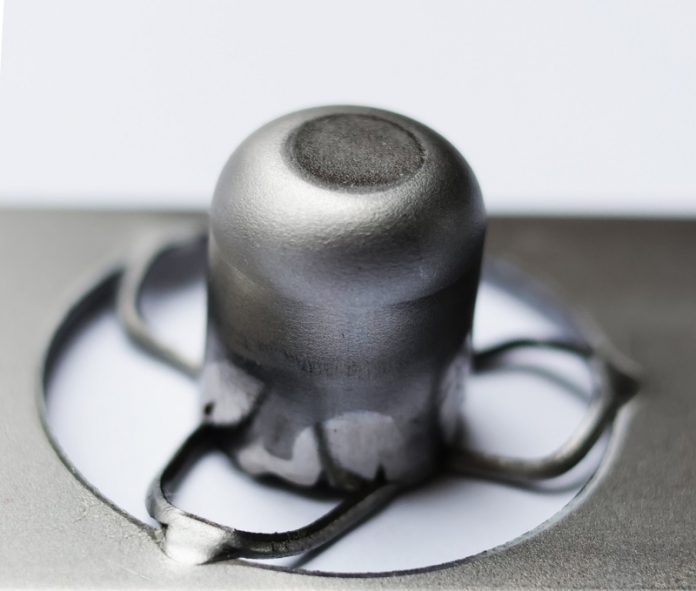
Many everyday items, from home appliances to building materials and hydraulic lines, contain small cylindrical metal parts made using deep drawing.
This manufacturing process involves shaping metal sheets into different forms.
However, this method can cause problems like material thinning, surface damage, or even cracks due to the strain involved.
Now, researchers have found a way to solve these issues using ultrasonic vibrations.
By integrating these vibrations into the deep drawing process, they have significantly reduced friction, making the process smoother and more efficient.
The new method, called VibroDraw, was developed by Fraunhofer IWU in partnership with MARK Metallwarenfabrik GmbH and DEVAD GmbH. It allows deep drawing to be performed at industrial speeds of up to 500 strokes per minute.
Ultrasound technology not only protects tools and materials but also reduces energy consumption.
This is great news for manufacturers who produce pipes and fittings, as lower friction means they can save energy and extend the life of their equipment.
Until now, using ultrasound in deep drawing was only effective in controlled laboratory settings.
However, M.Sc. Martin Mädlow and his team successfully adapted this technology for real-world industrial applications.
To generate ultrasonic vibrations, the researchers had to decide which part of the deep drawing tool should receive the vibrations.
They chose the die—the part responsible for shaping the metal—as it moves the most during the process. This choice has already led to a 20% reduction in friction, with even more improvements expected in the future.
Because friction is reduced, manufacturers can now form metal in fewer steps without causing damage. For example, instead of using three forming stages, they might only need two.
Less friction also results in lower heat generation, which means tools last longer, production speeds can increase, and lubricants stay cleaner for longer.
Fraunhofer IWU is working quickly to introduce this innovation to industrial manufacturing. Their current focus is on using ultrasonic deep drawing for making cell housings for high-voltage batteries in electric vehicles. This method allows for the production of larger battery cells that store more energy and improve driving range.
The technology is already on its way to becoming widely used. A patent application for VibroDraw (EPA WO2025/012830 A1) has been filed, marking an important step toward bringing this breakthrough to industries around the world. With its ability to cut friction, save energy, and extend tool life, ultrasonic deep drawing could revolutionize metal forming in the future.