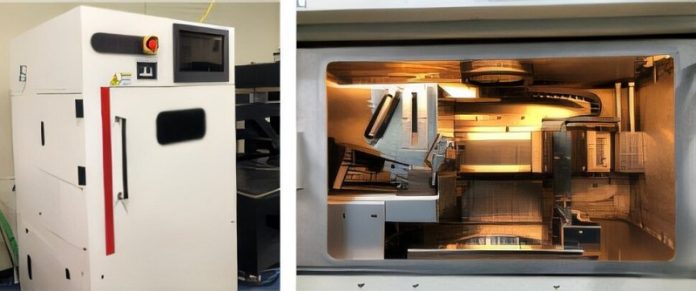
Scientists in South Korea have made an exciting breakthrough in motor manufacturing by using magnetic 3D printing technology.
This innovation, developed by the Korea Institute of Machinery & Materials (KIMM), allows the creation of high-performance motors without the need for traditional molds.
It’s the first time such technology has been achieved in South Korea, opening the door to more efficient, flexible, and cost-effective motor production.
The research team, led by Dr. Taeho Ha from KIMM’s Department of 3D Printing, worked alongside experts from the Korea Institute of Materials Science and Gachon University.
Together, they developed a complete solution for designing and creating motors using magnetic 3D printing.
This approach allows manufacturers to overcome the limits of traditional methods by enabling complex motor designs that weren’t possible before.
At the heart of the innovation is custom 3D printing equipment that enhances the magnetic properties of materials.
This eliminates the need for molds and allows the production of motors with improved performance in the same size.
The team demonstrated this with a 500-watt motor, achieving an impressive output density of more than 2.0 kW per liter.
Traditional motors are typically made using methods like electrical steel lamination or powder forming, which rely on molds.
These methods come with significant downsides, including high costs, material waste, and design restrictions. The use of molds also limits the flexibility and performance of the final product.
Magnetic 3D printing solves these issues by removing the need for molds entirely. It allows for the creation of intricate designs that maximize motor performance, all while reducing waste and cutting production costs.
This technology is particularly well-suited for axial flux motors, which are known for delivering high torque and output in small spaces. Such motors are ideal for applications in robotics, electric vehicles, and medical devices.
As industries increasingly demand smaller, more powerful, and more efficient motors, magnetic 3D printing offers a promising solution.
The flexibility of this technology means it can be applied to various fields, including robotics, future mobility solutions, and even healthcare devices. By simplifying the production process, it also supports the growing trend of small-batch, multi-variety production, making it easier to meet diverse needs.
Dr. Ha describes this technology as a leap forward, saying, “Magnetic 3D printing is an innovative step beyond traditional methods, unlocking new possibilities for next-generation high-performance motors.”
The team plans to continue advancing this technology by combining it with other 3D printing techniques for functional materials, aiming to expand its applications to more advanced industrial fields.
This breakthrough not only improves motor performance but also sets the stage for a more sustainable and cost-effective future in manufacturing.
Source: KSR.