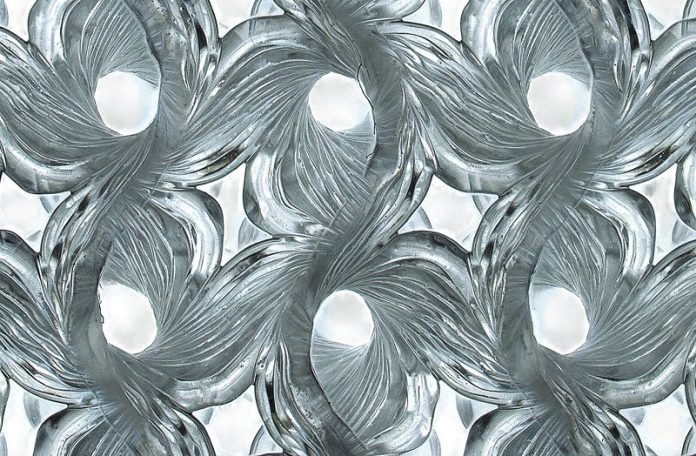
Researchers at Lawrence Livermore National Laboratory (LLNL) have developed a new silicone-based ink that could transform 3D printing.
This breakthrough allows for creating larger, taller, thinner, and more complex silicone structures than ever before, solving challenges that have long limited silicone printing.
The innovative “fast cure” silicone ink, featured in Advanced Materials Technologies, is a game-changer for 3D printing, particularly for silicone, a versatile material widely used in protective gear, biomedical devices, flexible electronics, and soft robotics.
What makes this ink special?
The new silicone ink combines simplicity with cutting-edge technology.
It’s a two-part system: one part contains a crosslinker (which binds molecules together) and the other a catalyst (which speeds up chemical reactions).
These components are kept separate until the moment of printing, where they mix inside the nozzle of the printer. This process, called inline mixing, causes the ink to gel and solidify almost instantly as it’s printed.
This approach has several advantages:
- No Time Pressure: Unlike traditional silicone inks, the new formula won’t harden in the syringe, giving users unlimited time to complete a print.
- Improved Stability: The ink sets quickly after being printed, meaning the structure won’t sag or collapse, even in challenging shapes.
- Simpler Process: There’s no need for extra steps like baking the material in an oven to cure it, streamlining the production process.
“We’ve made a method that’s easy to use and reliable,” said Dr. Anna Güell Izard, lead author and postdoctoral researcher at LLNL. “You don’t need to worry about the ink setting too soon or your design failing halfway through.”
The fast-curing ink enables designs that were previously impossible to achieve with silicone. Traditional 3D printing methods struggled with tall, thin, or complex shapes because the material couldn’t support its weight. However, the new ink allows researchers to print intricate structures, like cubic lattices with 90% porosity (lots of empty space) and unsupported overhangs, that hold their shape perfectly.
Dr. Güell Izard and her team put the new ink to the test, printing delicate designs like tall slender towers, intricate lattices, and sharp overhanging angles. Structures that would have collapsed using traditional inks emerged fully intact with the new formula.
“The results were amazing,” said Dr. Güell Izard. “What we printed came out of the oven exactly as designed, with walls totally firm. It felt like we’d unlocked something magical.”
The next step for the team is to fine-tune the ink for even more applications. For example, adjusting the catalyst levels could control the speed at which the ink gels, opening up new possibilities for taller and more complex designs.
The researchers also plan to explore how the method could be adapted to other materials, potentially enabling a wide range of new 3D printing applications.
“This discovery shows how far we can push 3D printing,” said Dr. Güell Izard. “From medical devices to robotics, this technology could revolutionize industries and inspire entirely new applications.”
The breakthrough not only expands the potential of silicone in 3D printing but also opens the door to more efficient, precise, and creative manufacturing techniques in the future.