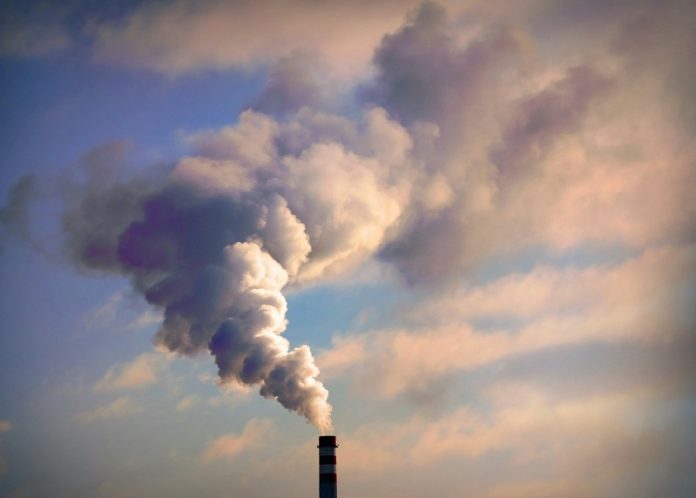
Industrial plants like cement and steel factories produce large amounts of carbon dioxide (CO₂), a major greenhouse gas.
However, their emissions are often too hot for current carbon capture technologies, which need a lot of energy and water to cool down the exhaust.
This has made it hard to apply CO₂ capture in some of the most polluting industries.
Now, scientists at the University of California, Berkeley, have developed a new material that can capture CO₂ directly from these hot exhaust streams.
This material, a special type of metal-organic framework (MOF), acts like a sponge to trap CO₂ at high temperatures.
The breakthrough, published in the journal Science, could revolutionize how we approach industrial carbon capture.
The most common way to capture CO₂ today involves using liquid amines, which react with CO₂ to remove it from emissions.
However, this method only works efficiently at temperatures between 40°C and 60°C (100°F–140°F).
Exhaust from cement and steel plants, on the other hand, can exceed 200°C (400°F), making current methods impractical. Cooling these hot gases requires costly infrastructure and large amounts of energy.
Even newer materials designed to work at higher temperatures often fail or degrade above 150°C (300°F). This has left a significant gap in carbon capture technology for industries with high-temperature emissions.
The UC Berkeley team, led by postdoctoral fellow Kurtis Carsch and graduate student Rachel Rohde, developed a MOF that can trap CO₂ even at extreme temperatures up to 300°C (570°F). Unlike traditional amine-based systems, this material uses zinc hydride sites in its porous structure to bind CO₂. These sites are highly stable and effective, even under the intense conditions found in industrial plants.
MOFs are unique materials with a crystalline structure made of metal ions and organic molecules. Their porous design provides an enormous surface area—comparable to six football fields per tablespoon—making them ideal for capturing gases.
Under simulated conditions, the new MOF was able to trap CO₂ from industrial exhaust streams containing 20–30% CO₂, like those in cement and steel manufacturing. It also worked well with the lower CO₂ concentrations (around 4%) found in natural gas power plants.
Capturing CO₂ from industrial emissions is essential for fighting climate change. While renewable energy reduces the need for fossil fuels in power plants, industries like steel and cement are harder to make sustainable. This new MOF could play a vital role in decarbonizing these sectors by capturing up to 90% of CO₂ emissions.
Once the MOF is full of CO₂, the gas can be removed by flushing it with another gas or applying a vacuum. The MOF can then be reused for another cycle of carbon capture.
The researchers believe their discovery could open new doors for high-temperature gas separation. They are now exploring ways to improve the MOF’s performance and adapt it for other gases.
“This material is a game-changer,” said Rohde. “It allows us to capture CO₂ under conditions that were previously thought impossible.”
As the fight against climate change continues, innovations like this offer hope for a more sustainable future, particularly in industries that have been difficult to clean up.