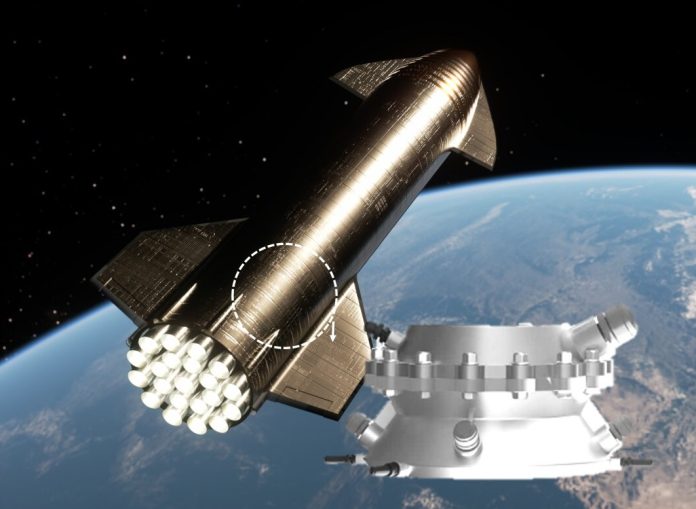
A team of researchers has developed a high-performance, 3D-printed metal alloy designed for the extreme conditions of space.
This new alloy is built to withstand the harsh cryogenic temperatures found in space, reaching as low as -196°C, and it shows great promise for use in space exploration and other extreme environments.
Led by Dr. Jeong Min Park from the Korea Institute of Materials Science (KIMS), in collaboration with Professor Jung Gi Kim of Gyeongsang National University and Professor Hyoung Seop Kim of POSTECH, the team created this unique alloy by adding a small amount of carbon to a base material called CoCrFeMnNi.
This combination enhances the alloy’s properties in very cold temperatures, making it stronger and more flexible than similar materials.
The process of creating this alloy involves a 3D printing technique known as Laser Powder Bed Fusion (LPBF).
This technique uses a laser to melt and fuse layers of metal powder, building up parts layer by layer. By carefully controlling the carbon content, the researchers were able to form tiny, evenly distributed nano-carbides within the alloy, which strengthen the material.
This precise control results in a nano-sized cell structure that adds durability and flexibility to the alloy.
The results were impressive: the new alloy showed a 140% improvement in both strength and flexibility compared to similar materials without carbon. Remarkably, its ability to stretch, or “elongation,” was twice as high at cryogenic temperatures (77 K) compared to room temperature (298 K).
This makes it especially suited for the intense conditions of space, where materials need to endure extreme cold without breaking.
The alloy’s durability at low temperatures also offers guidance for designing future alloys using 3D printing. Its ability to support heavy loads and withstand cryogenic conditions means it could be used to create stronger, longer-lasting parts for spacecraft, such as rocket fuel injectors and turbine nozzles, which operate under intense conditions.
This alloy overcomes the typical weakness of many 3D-printed metals, which often struggle with low-temperature toughness.
Dr. Park, the project leader, explained that this research opens up new possibilities for building components that exceed the limits of conventional space technology.
“This breakthrough in alloy development will help us produce stronger, longer-lasting parts for space launch vehicles, pushing the boundaries of what is possible in space exploration,” he said.
This innovation not only paves the way for improved space technology but also shows the potential of 3D printing in creating durable materials for extreme environments.
Source: KSR.