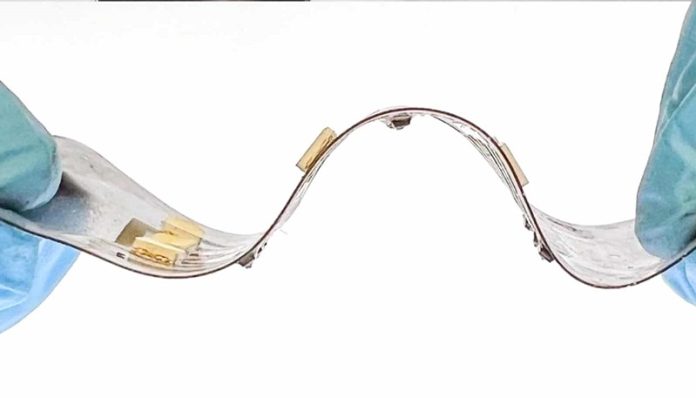
Researchers have discovered a new way to build flexible electronic connections that could pave the way for advanced soft robotics, wearable devices, and more durable electronics.
Imagine a phone or a health monitor made of soft materials that can bend and twist—this could change how we use and experience everyday electronics.
The team led by Michael Bartlett, an associate professor at Virginia Tech, has developed a technique that makes these ideas more achievable.
Their findings, published in Nature Electronics, focus on creating soft circuits that manage all the electronic connections inside devices.
The researchers used a novel approach involving liquid metal microdroplets to create tiny conductive pathways, called vias, which pass through and across circuit layers. Vias are crucial for connecting different layers in circuit boards.
Traditional methods require drilling holes through rigid materials to create these connections, but that doesn’t work for soft materials that can stretch and bend. Bartlett’s team solved this by developing a method that doesn’t require drilling.
“Our work brings us closer to exciting possibilities like advanced soft robotics, wearable devices, and electronics that can stretch, bend, and twist while maintaining high functionality,” Bartlett says.
The technique developed by the team uses liquid metal droplets that can move through circuit layers in a stair-like pattern.
This method forms tiny connections without making holes, which is a big improvement over previous techniques. The liquid metal droplets are embedded in a photoresin, a material that solidifies under ultraviolet (UV) light.
During the process, the researchers take advantage of slight imperfections that occur when exposing the photoresin to UV light. These imperfections, known as mask-edge abnormalities or undercutting, usually cause problems in traditional electronics manufacturing.
However, Bartlett’s team turned this challenge into an advantage.
The edges created during UV exposure guide the liquid metal droplets into forming a stair-like structure, which allows the droplets to settle in a controlled, 3D pattern. This creates continuous pathways connecting the top and bottom layers of the circuit.
The result is a quick and versatile process that allows for the creation of flexible circuit layers in a matter of minutes. According to Bartlett’s colleague, Dong Hae Ho, a postdoctoral researcher, this technique maintains both the flexibility and strength of the soft device. “By leveraging these otherwise unwanted edge effects, we can create soft, conductive vias that connect different circuit layers in a rapid and parallel fashion,” he explains.
By integrating these soft circuits with multiple layers, the team can build complex and flexible electronics. This opens up new possibilities for creating devices with sophisticated multilayer designs, which is essential for developing advanced soft electronics.
The researchers from Virginia Tech collaborated with scientists from the University of Pennsylvania, and their work received support from several sources, including the Office of Naval Research and the National Science Foundation.
This breakthrough method could one day lead to more flexible, durable, and user-friendly electronic devices in healthcare, robotics, and everyday technology.