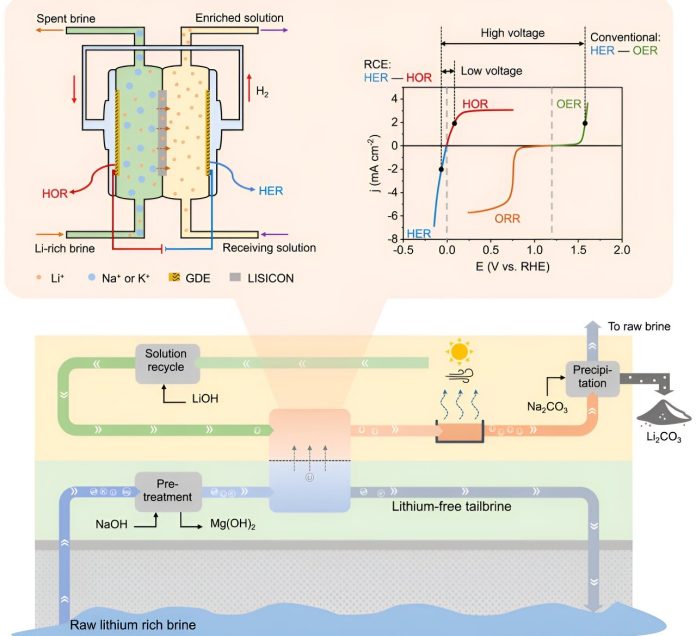
A groundbreaking new technology developed by researchers at Stanford University could change the way lithium is extracted from brines.
This method promises to be much cheaper and more environmentally friendly than the current dominant method, offering a potential game-changer for the lithium industry.
According to a study published in the journal Matter, this new technique could extract lithium at just 40% of the cost of today’s methods and at a fraction of the current market price.
Lithium is a critical component in the production of batteries for electric vehicles and renewable energy storage systems.
As the demand for these technologies grows, so does the need for lithium. In fact, global demand for lithium is expected to skyrocket from about half a million metric tons in 2021 to between 3 and 4 million metric tons by 2030.
Traditionally, lithium has been extracted in two main ways: from mined rocks or from brines, which are salty waters found in certain lakes, hot springs, and as a byproduct of oil and gas production.
The brine method involves evaporating the water in large ponds over a year or more, leaving behind a lithium-rich solution. However, this method is costly, time-consuming, and has significant environmental downsides, including heavy water use and reliance on toxic chemicals.
The new method developed by the Stanford team uses an approach called “redox-couple electrodialysis” or RCE. This technique uses electricity to move lithium through a solid-state membrane from a low concentration in the water to a high-purity solution.
The process is highly efficient, with a lithium selectivity of almost 100%, meaning it can precisely separate lithium from other elements.
The researchers estimate that this method could produce high-purity lithium hydroxide for $3,500 to $4,400 per ton, compared to the $9,100 per ton cost of current brine extraction methods.
This method also uses significantly less electricity—less than 10% of what’s needed for current brine extraction techniques—and doesn’t require the large evaporation ponds that take up vast amounts of land.
By avoiding these ponds, the RCE method reduces the environmental footprint of lithium extraction and makes the process more sustainable.
While the RCE method shows great promise, there are still some challenges to overcome before it can be widely adopted.
For instance, the current technology has a battery life of about 30 minutes, and scaling it up to industrial levels will require further refinement. However, the researchers are optimistic that these issues can be resolved, making this method a viable alternative to existing extraction techniques.
The team has already tested the RCE method with various types of saline waters, including those with different concentrations of lithium, sodium, and potassium. They even explored extracting lithium from wastewater produced by oil extraction, and they believe the method could potentially be adapted to extract lithium from seawater—a resource with much lower lithium concentrations than brines.
As the demand for lithium continues to rise, the need for more efficient, cost-effective, and environmentally friendly extraction methods becomes increasingly urgent. The RCE method developed by the Stanford team could play a crucial role in meeting this demand while minimizing the impact on our planet.
The researchers are now focused on optimizing the design of their device and testing other promising materials for the membrane to further improve the efficiency and scalability of the technology.
If successful, this method could soon move from the lab to large-scale industrial applications, offering a sustainable solution to the growing global demand for lithium.