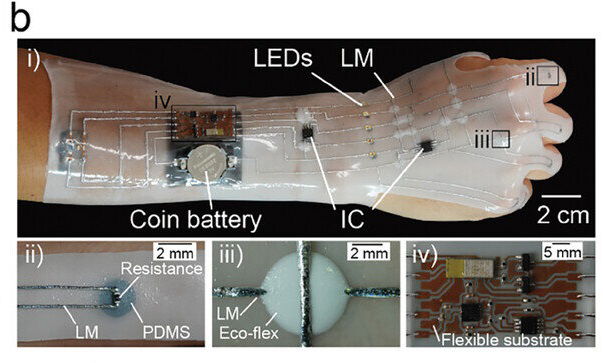
Electronics have come a long way from simply enhancing our daily lives to becoming an essential part of them.
We are already familiar with wearable electronics, but what about stretchable ones?
These flexible devices could become a reality for everyday use thanks to a new mass production method called the roll-to-roll (R2R) process.
The current demand for stretchable electronics is high, but the existing methods for making them are not suitable for large-scale production.
The R2R process, which prints various layers on a flexible rolled substrate, could change that.
By using this method, it is possible to produce stretchable electronics and even smart packaging on a large scale, making them more accessible to the public.
Researchers published their findings in Advanced Materials Technologies. Traditional methods can create complex, multilayered patterned substrates, but they lack the capacity for large-scale production.
As technology advances, the need for newer and better electronics grows, making it necessary to adapt production methods.
“In this study, we focused on developing the R2R production process for mass production of stretchable devices,” said Hiroki Ota, associate professor at Yokohama National University and author of the paper. “These technologies are crucial for bringing stretchable electronics, which are still in the research phase, to the market.”
The R2R production process involves creating elastic substrates with multiple material layers and embedded electronics. This method allows for continuous production, using materials like hydrogels or silicone, and liquid metal wiring. The process includes coating and preparing the material for wiring, resulting in a flexible, elastic, and functional product.
Previously, the R2R process was used for newspapers and photography, but now it is being employed for manufacturing electronics such as organic solar cells and flexible electronic substrates. This technology could pave the way for large-scale production of stretchable electronics, including wearables, smart packaging, and soft electronics.
In the study, 15 stretchable devices with light detection were produced and tested for their ability to respond to light levels while being stretched. These materials maintained functionality even when stretched by 70% of the substrate’s maximum. Additionally, devices equipped with thermistors (tools used to measure temperature) provided accurate readings compared to the actual set temperatures.
“The R2R process technology has not yet realized stretchable wiring, but in the future, by linking the R2R production process for liquid metal wiring and substrates, we can achieve continuous and mass production of stretchable devices,” said Ota.
The evolution of the R2R process offers many opportunities for stretchable electronics and devices. So far, R2R processing on elastic materials has achieved accuracy and consistent performance when stretched. Researchers hope to see further developments in micropattern fabrication for higher resolution and improved functionality of the process and its outcomes.
With these advancements, stretchable electronics could soon become a common feature in our daily lives, providing new possibilities for wearable technology and smart packaging.