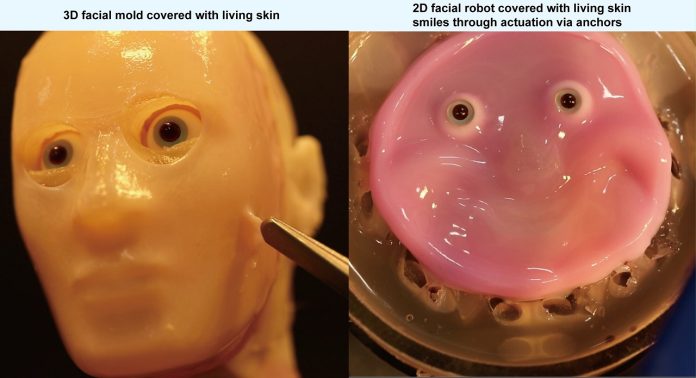
Imagine robots that can heal themselves and move with lifelike grace.
Researchers have found a way to attach engineered skin tissue to the complex shapes of humanoid robots, giving them incredible new abilities like self-healing, embedded sensing, and a more human appearance.
This breakthrough could lead to more advanced robots that can help in various fields, from medicine to cosmetics.
The research team, led by Professor Shoji Takeuchi from the University of Tokyo, took inspiration from human skin ligaments.
They included special perforations in a robot’s face, allowing a layer of engineered skin to firmly attach. Their findings are published in the journal Cell Reports Physical Science.
Professor Takeuchi is a leader in biohybrid robotics, a field where biology and mechanical engineering come together.
His lab, the Biohybrid Systems Laboratory, has created mini robots that walk using biological muscle tissue, 3D-printed lab-grown meat, and engineered skin that can heal. It was during their research on engineered skin that Takeuchi saw the need to improve how this skin attaches to robotic features.
Previous methods of attaching skin tissue to solid surfaces involved mini anchors or hooks, which limited the types of surfaces that could receive skin coatings and often caused damage during movement.
Takeuchi’s team developed a new method by mimicking human skin-ligament structures. They used specially made V-shaped perforations in solid materials, allowing the skin to move with the robot without tearing or peeling away.
“During previous research on a finger-shaped robot covered in engineered skin tissue we grew in our lab, I felt the need for better adhesion between the robotic features and the subcutaneous structure of the skin,” Takeuchi said.
Their new anchoring method allows flexible skin tissue to conform to any shape it’s attached to. For example, a flat robotic face can smile and the skin deforms naturally, then returns to its original shape.
This method can work on complex, curved, and even moving surfaces.
The researchers used a special collagen gel for adhesion, which is naturally viscous and difficult to feed into tiny perforations.
By using a common plastic adhesion technique called plasma treatment, they managed to coax the collagen into the fine structures of the perforations while also holding the skin close to the surface.
Manipulating soft, wet biological tissues during development is challenging. If sterility is not maintained, bacteria can enter and the tissue will die. However, the team’s new method overcomes these obstacles, allowing living skin to bring new abilities to robots.
Living skin can self-heal, a significant advantage over chemical-based materials that require triggers like heat or pressure to repair themselves. Biological skin repairs minor cuts and can be enhanced with nerves and other organs for sensing.
Takeuchi’s research aims to help in several areas of medical research. For example, a “face-on-a-chip” could be useful in studying skin aging, cosmetics, surgical procedures, and plastic surgery. If sensors can be embedded, robots may gain better environmental awareness and improved interactive capabilities.
“In this study, we managed to replicate human appearance to some extent by creating a face with the same surface material and structure as humans,” Takeuchi said. “However, we identified new challenges, such as the need for surface wrinkles and a thicker epidermis to achieve a more humanlike appearance.”
The team believes that creating a thicker and more realistic skin can be achieved by incorporating sweat glands, sebaceous glands, pores, blood vessels, fat, and nerves. Movement is also crucial, so another challenge is creating humanlike expressions by integrating sophisticated actuators, or muscles, inside the robot.
Creating robots that can heal themselves, sense their environment more accurately, and perform tasks with humanlike dexterity is incredibly motivating. This research opens up exciting possibilities for the future of robotics, making them more lifelike and capable of a wide range of applications.