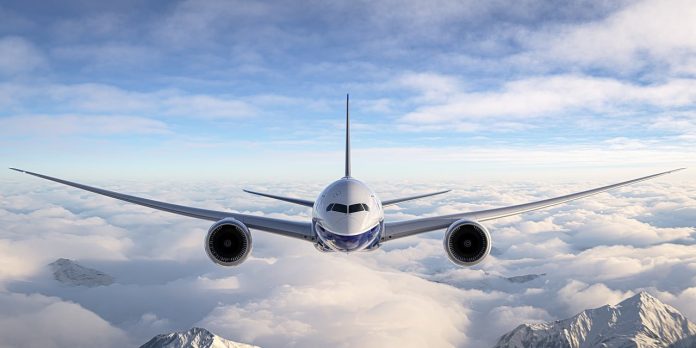
The aviation industry is striving to reduce its environmental impact, and additive manufacturing (AM) is playing a crucial role in this effort.
However, for AM to meet the industry’s high safety and quality standards, a deep understanding of the process is necessary.
New research by Karthikeyan Thalavai Pandian at University West in Sweden is helping to bridge this gap.
Modern aircraft already use engine components made with AM, but mostly for less critical parts. Given its many benefits, GKN Aerospace, a leading aircraft engine manufacturer, aims to use AM for more critical components in a variety of materials. This ambitious goal requires extensive research and rigorous testing.
Pandian’s doctoral dissertation, presented in late May, focuses on electron beam powder bed fusion (PBF-EB), a type of AM technology, for titanium alloys.
“Additive manufacturing is very exciting for making certain components. It reduces material use, lowers costs, and decreases environmental impact in the long run. Plus, it allows for the creation of complex shapes that are impossible with traditional methods like casting and forging,” explains Pandian.
His research has mainly looked at the microstructure and mechanical properties of the titanium alloy Ti-6Al-4V. This alloy is used in the low-temperature sections of aircraft engines because of its high strength.
“My research focuses on improving the fatigue properties of PBF-EB-built Ti-6Al-4V material. When using AM, surface quality and defects can impact fatigue properties. Rough and uneven surfaces can reduce the fatigue performance of components.
Several PBF-EB process parameters can make surfaces too rough and uneven. I have explored how some of these parameters affect surface roughness and how PBF-EB-built surfaces influence fatigue properties,” he says.
“Similar to surface roughness, defects in the bulk of AM components can be harmful to their fatigue life.”
AM-built components typically undergo post-build heat treatments, such as hot isostatic pressing. However, current methods were developed for conventional manufacturing and are not optimal for AM, as they can weaken the material.
“I have investigated a new heat treatment method tailored for AM. This method uses a lower temperature, which offers several advantages: the titanium alloy does not lose strength, and the fatigue properties are as good as the standard method,” Pandian continues.
For the aviation industry to adopt this new method, it must be standardized according to the industry’s safety and quality criteria.
“Once a standard is established, the industry can more efficiently use AM to make more components. This technology is also interesting for other fields, like the medical industry that makes implants,” Pandian notes.
One of Pandian’s main goals is to develop AM technology that reduces the need for post-build machining while still meeting quality requirements. This can be done by improving the surface quality of AM-built components.
“By reducing the post-build machining depth from about 2 mm to 1 mm, we save material and time. If we can build components that don’t need any post-processing, we can truly say we’ve created a sustainable manufacturing method. Today we talk about ‘near-net-shape,’ but the goal should be ‘net-shape,'” says Pandian.
Now a senior lecturer at University West, Pandian continues his research while teaching. “I look forward to working with more AM processes and materials, focusing on fatigue properties and ensuring quality with the help of AI.”
After eleven years as a product developer at Volvo Construction Equipment in India, Pandian realized the importance of understanding how material properties affect the final product. “Now, after completing my doctoral studies, I am convinced that more research in materials science can make a big difference,” he concludes.
Pandian’s work brings us one step closer to making aviation more sustainable through advanced manufacturing techniques.