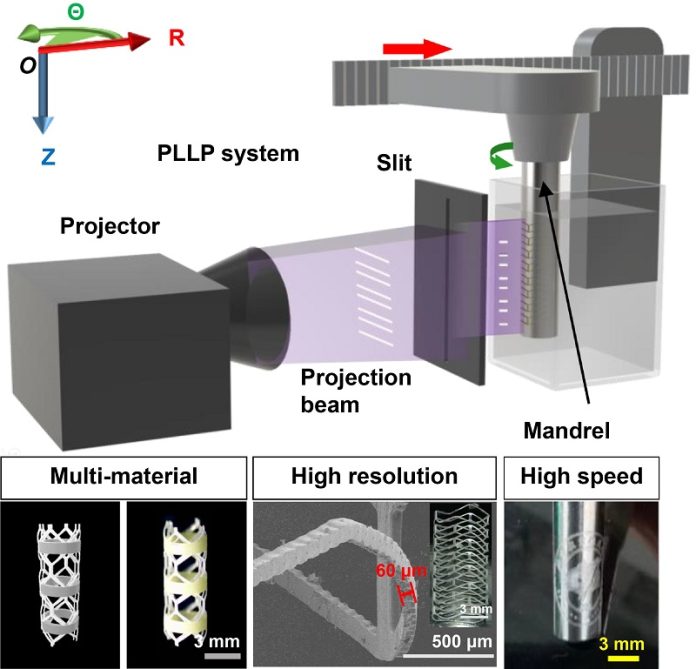
Researchers from Beihang University have developed an innovative 3D printing technology capable of creating extremely thin tubular structures, potentially transforming industries like biomedical engineering, dentistry, and aerospace.
Their groundbreaking work, published in the International Journal of Extreme Manufacturing, introduces a method that can print tubes with walls as thin as 50 micrometers—slimmer than a human hair—and features as small as 10 micrometers.
Traditional methods of manufacturing such delicate and complex structures have faced significant challenges, particularly when it comes to creating tubes with multiple materials.
These multi-material tubes, which can have varying mechanical properties, are essential for applications like vascular grafts in medical treatments or lightweight components in aerospace engineering.
Professor Jiebo Li, the lead researcher and a professor in the School of Biological Science and Medical Engineering at Beihang University, explained that most existing 3D printing technologies are not suited for this task.
They typically rely on a Cartesian coordinate system, which is effective for simpler, non-tubular shapes but falls short with cylindrical structures that require high precision and smooth surfaces.
To address this, the team developed a new approach using polar coordinates. Their system, known as Polar-coordinate Line-projection Light-curing Production (PLLP), employs a rotating mandrel that acts as the base for the printing process.
This setup allows for the light to cure or harden a liquid polymer into the desired thin-walled tube shape as the mandrel turns.
This method vastly improves on traditional techniques by eliminating the need for supporting structures that can interfere with the smoothness and integrity of the final product.
The rotating mandrel enables continuous printing without the instability issues that come with high aspect ratios, such as a small tube diameter compared to its length, which can make the structure difficult to support and maintain during the printing process.
The Beihang team has demonstrated that their PLLP technology not only creates tubular structures with unprecedented precision but also does so faster and more effectively than existing methods.
They have successfully tested the printing of hydrogel materials, which are often used in biomedical applications, confirming the versatility and effectiveness of their approach.
Looking ahead, the researchers are focused on further refining their technology to enhance the printing speed and resolution even more.
Their goal is to expand the use of PLLP technology across various fields, offering customized solutions for complex tubular structures that meet specific industry needs.
This innovation opens up new possibilities for manufacturing intricate tubular components with ease and precision, heralding a new era in 3D printing technology that could have far-reaching implications across multiple sectors.
Source: KSR.