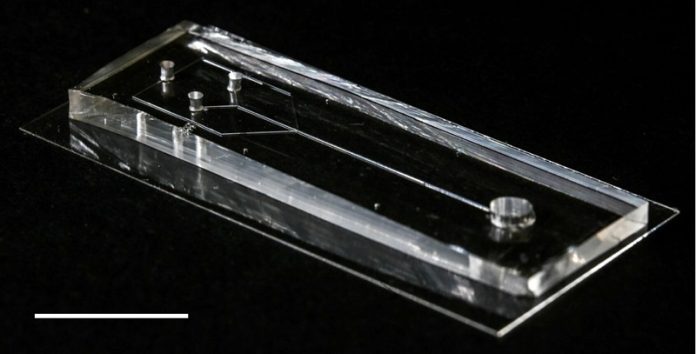
In Japan, scientists have made an exciting breakthrough.
They’ve created a machine that can make spider silk, a material known for being super strong, flexible, and light. This artificial silk is just like what real spiders make.
This big step, led by Keiji Numata and his team at the RIKEN Center for Sustainable Resource Science, could be great news for the environment and many industries.
Their work was published in the journal Nature Communications.
Spider silk is amazing. It’s as strong as steel but much lighter, and it’s also safe to use in medical treatments and can break down naturally. But why don’t we see spider silk everywhere? Getting a lot of silk from spiders isn’t easy, so scientists have been trying to make it in labs.
Spider silk is a special kind of fiber made of big proteins with repeating parts, known as spidroins. The silk gets its unique strength from tiny structures inside it, called beta sheets, which need to be aligned just right. Making this complex structure in the lab has been a tough challenge for scientists.
Instead of starting from scratch, the RIKEN team used a method called biomimicry. This means they tried to copy how nature does it. Numata says, “We looked at how spiders naturally make silk. They use something like a tiny fluid-moving device. We made a similar small box with narrow channels to do this.”
In their device, a liquid with the silk proteins is placed at one end and then gently pulled to the other end. As this liquid moves through the channels, it undergoes changes in its environment, set up by the design of the system. Under the right conditions, the proteins join together to form silk fibers with the same complex structure as natural spider silk.
The team found that using negative pressure (like a gentle pull, rather than a push) was key to making continuous silk fibers with the correct structure. Senior Scientist Ali Malay, who worked on the project, said, “Once we figured out the right conditions, making the silk was quick, reliable, and the fibers looked just like natural silk.”
This new way of making silk could be really helpful. It could make textile production less harmful to the environment and offer a natural, safe material for medical uses like stitches and artificial body parts.
Numata says, “We want our work to make a difference in the real world. To do that, we need to produce more silk in a non-stop way. We’ll also check how good our artificial silk is and keep improving it.”
This discovery isn’t just a scientific achievement; it’s a step towards a more sustainable and environmentally friendly future, showcasing how mimicking nature can lead to remarkable innovations.