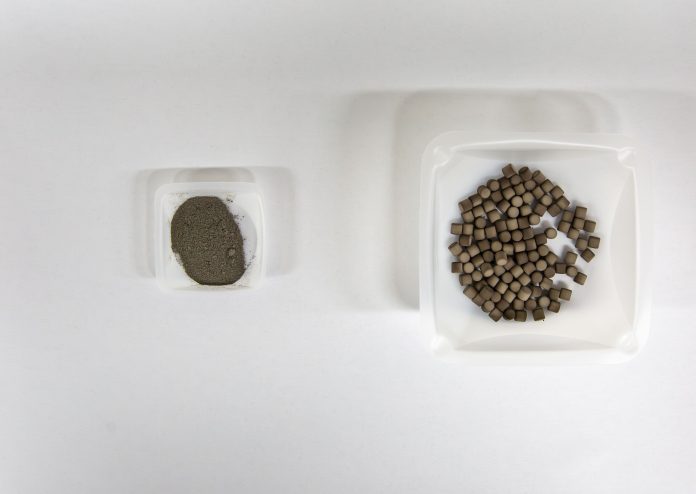
A team of scientists in South Korea has developed a new, more affordable way to produce hydrogen from ammonia—a breakthrough that could help speed up the move toward a clean hydrogen-powered future.
The research, led by Dr. Kee Young Koo from the Korea Institute of Energy Research (KIER), was recently published in the journal Small.
Ammonia, made up of one nitrogen atom and three hydrogen atoms, is already widely used around the world, and it’s now being looked at as a promising way to store and transport hydrogen.
Thanks to existing global infrastructure, ammonia is seen as a cost-effective carrier for hydrogen, especially for long-distance transport.
However, turning ammonia back into hydrogen when and where it’s needed remains a technical challenge.
To do this, scientists rely on special materials called catalysts to break ammonia molecules apart and release the hydrogen.
The most effective catalyst so far is ruthenium, a rare metal that can make this reaction happen at relatively low temperatures of around 500 to 600°C.
That’s more than 100°C lower than what other catalysts require, making ruthenium highly valuable.
But ruthenium is expensive and hard to get, which limits how widely it can be used. To make the most of it, scientists have been using ruthenium in tiny particles called nanoparticles.
These work well, but they are costly and complicated to produce, which has made it difficult to develop affordable and scalable systems for hydrogen production from ammonia.
Dr. Koo’s team tackled this problem with a fresh approach. They used a method called the polyol process, which is commonly used to create nanoparticles.
Usually, this process needs additional chemicals—called capping agents—to stop the nanoparticles from clumping together. But these chemicals make the process more expensive and harder to scale up.
Instead, the researchers found a simpler way to prevent clumping by carefully selecting the type of organic liquid used in the process.
They discovered that butylene glycol, which has a longer carbon chain, can control how the nanoparticles form and spread. This allowed them to make ruthenium particles just 2.5 nanometers in size, evenly dispersed without any extra additives.
Even more impressive, the new catalyst outperformed existing ones in several key ways. It reduced the energy needed to start the reaction by about 20% and boosted the hydrogen production rate by 1.7 times. Overall, when measuring performance by volume, the new catalyst was over three times more efficient than traditional versions.
Dr. Koo believes this innovation could solve a major problem in the push for clean hydrogen energy. “Our new catalyst offers a practical, cost-effective path toward mass-producing hydrogen from ammonia,” he said. “It brings us closer to commercializing this technology and producing hydrogen cleanly and efficiently.”
The team now plans to scale up production and test the new catalyst in real-world ammonia cracking systems to confirm its performance. If successful, this could play a major role in building a sustainable hydrogen economy.