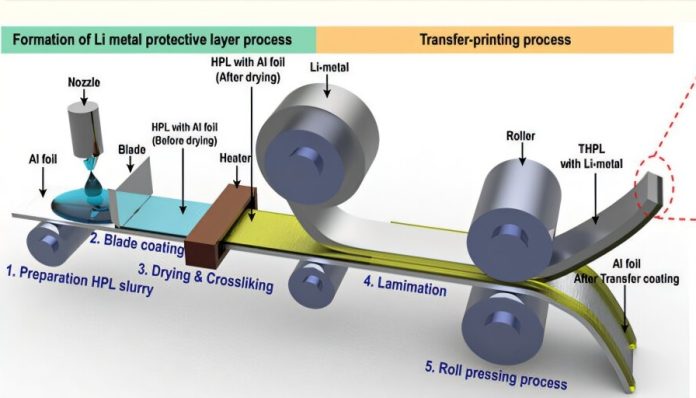
A team of researchers in South Korea has developed a new way to make lithium-metal batteries safer, longer-lasting, and closer to commercial use.
This innovation could help power the future of electric vehicles and large-scale energy storage.
Led by Dr. Jungdon Suk at the Korea Research Institute of Chemical Technology (KRICT), the team created a special transfer printing method that forms protective layers on lithium metal surfaces.
This new approach avoids the use of harmful solvents and prevents damage to the sensitive lithium, solving some of the biggest problems that have held back lithium-metal battery development for years.
Lithium-metal batteries are considered the next big thing in energy storage.
Unlike regular lithium-ion batteries, which use graphite as the anode (the negative side), lithium-metal batteries use pure lithium, which has ten times the capacity. That means much more energy packed into a smaller, lighter battery.
These batteries are key to developing advanced solid-state and lithium-sulfur batteries.
However, lithium metal has a major drawback. During charging and discharging, tiny needle-like structures called dendrites can form on its surface. These can grow large enough to cause short circuits, fires, or even battery failure.
Traditional ways of coating lithium with protective layers often involve liquid chemicals, which can introduce impurities and damage the lithium, making large-scale production very difficult.
The KRICT team tackled this by designing two types of protective layers: one made of alumina and gold, and another made from a mix of ceramic and flexible polymers.
Instead of coating the lithium directly, they created the protective layer on another surface, then gently transferred it onto the lithium using pressure—like applying a sticker. This process, called roll-to-roll transfer printing, is clean, scalable, and avoids damaging the lithium.
Their hybrid protective layers are just 5 micrometers thick but cover large areas evenly. These layers help stop dendrites from growing and ensure that lithium ions move smoothly between the electrode and the electrolyte during battery operation.
In battery tests, cells with the protective layer kept over 81% of their capacity after 100 charging cycles—more than twice as long as unprotected lithium—and remained highly stable even under fast charging.
The researchers believe this method could lead to commercial lithium-metal batteries that are safer and more efficient, especially for electric cars and energy storage systems. It could also be adapted for other advanced battery types like solid-state and lithium-sulfur batteries.
“This is one of the most practical solutions for making high-energy lithium-metal batteries a reality,” said KRICT President Dr. Young-Kuk Lee, noting the potential for this technology to strengthen South Korea’s position in the global battery industry.
Source: KSR.