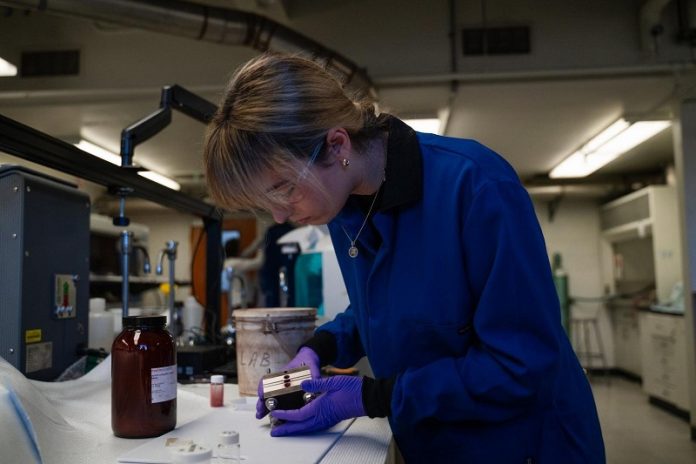
Scientists at the University of Oregon are working on a greener way to make iron metal—a big step toward cleaning up the steel industry, which is one of the largest sources of carbon pollution worldwide.
Their latest research, published in ACS Energy Letters, shows how this new method could be more efficient and environmentally friendly than the traditional way of making steel.
Right now, making iron from iron ore usually happens in blast furnaces that burn fossil fuels and release a lot of carbon dioxide into the air.
But chemist Paul Kempler and his team have developed a new method that uses saltwater and iron oxide (a natural form of iron found in the earth) to produce iron through electrochemical reactions.
This process also makes chlorine, which is a useful byproduct.
In their newest study, the team focused on finding the best kinds of iron oxide to use.
They wanted to understand what makes some materials better than others for producing iron.
At first, they thought it might be the size of the particles, the chemical makeup, or even the impurities. But after testing different samples, they discovered that what really matters is how porous the material is—how many tiny holes it has.
The porous iron oxide particles have a larger surface area, which helps the chemical reactions happen faster.
In contrast, denser particles with fewer holes slowed things down. This matters a lot because large-scale electrochemical plants are expensive to build, and making iron quickly helps reduce the cost of the final product.
The team’s key insight is that surface area—not particle size—is crucial. The more porous the material, the faster and more efficiently it can produce iron.
And while they used a specific type of nanoparticle in their lab tests, the same principle could apply to many other low-cost, naturally available iron oxides.
Kempler’s group is now working with engineers and manufacturers to figure out how to scale up this process for real-world use. They hope this cleaner method can one day replace the traditional, more polluting way of making iron.
Graduate student Andrew Goldman summed it up well: “We can still have the benefits of modern industry without hurting the planet. It’s not perfect yet, but it’s a start—and that’s exciting.”
The ultimate goal is simple: make iron in a way that’s cheap, efficient, and far less harmful to the environment. If successful, it could reshape one of the world’s most important industries.