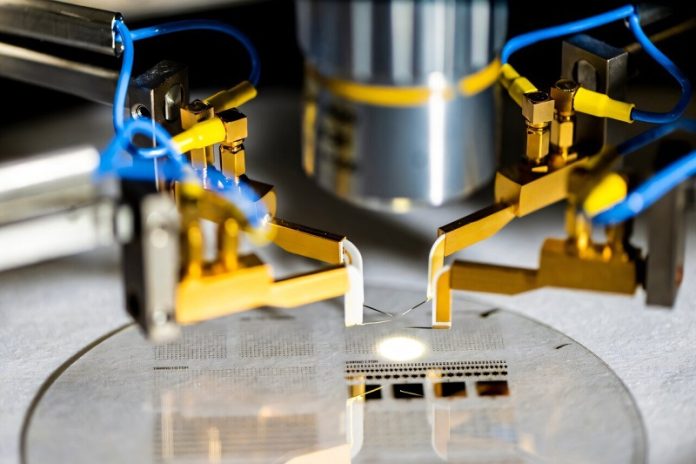
A professor at Northeastern University has developed a revolutionary new way to manufacture microchips, cutting costs by 99% and making the process much faster and more efficient.
Traditional chip manufacturing is incredibly expensive and slow.
Factories, known as “fabs,” cost between $20 billion and $40 billion to build, and running them requires over $1 billion each year.
They also use enormous amounts of energy—enough to power 50,000 homes. Due to these high costs, the number of companies making advanced chips has dropped significantly over the years.
But Professor Ahmed A. Busnaina, who leads the National Science Foundation Center for High-rate Nanomanufacturing at Northeastern University, has developed a new method that works in a completely different way.
Instead of the traditional process, which involves depositing layers of material and then etching away the excess, his approach only adds the material needed in the right places.
This “bottom-up” technique is similar to sculpting with clay instead of chiseling from stone.
This new method dramatically reduces waste, speeds up production, and lowers costs. Busnaina and his team have shown that they can create incredibly tiny structures—just 25 nanometers in size—within a minute, covering large areas quickly and efficiently.
This breakthrough could change the entire chip industry. With this technology, chip manufacturing could become as easy as making photocopies at a print shop.
Instead of waiting six months to a year to get a chip manufactured, designers could bring their plans to a specialized 3D printing shop and have their chip produced the same day or the next.
“Imagine if every chip designer could get their design made within a week, test it, and refine it quickly,” Busnaina says. “This will not only democratize chip manufacturing but also speed up innovation and make electronics much more affordable.”
This new nanomanufacturing process has the potential to revolutionize the electronics industry, making it easier for startups, researchers, and businesses to create new technology without the massive costs and delays of traditional chip production.