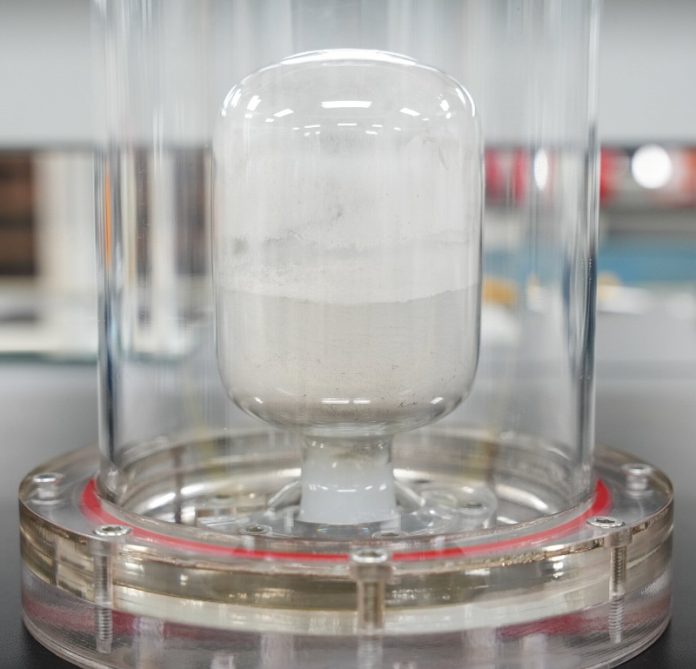
A research team led by Dr. Ha Yoon-Cheol at the Korea Electrotechnology Research Institute (KERI) has made an exciting breakthrough in battery technology.
They have developed a new method to produce high-quality lithium superionic conductors more quickly and affordably.
This innovation could help speed up the development of all-solid-state batteries (ASSBs), which are safer and more efficient than traditional lithium-ion batteries.
Batteries today mostly use liquid electrolytes, which transfer ions between the positive (cathode) and negative (anode) sides of the battery.
However, liquid electrolytes can pose safety risks, including leaks, fires, and explosions.
ASSBs replace the liquid with a solid electrolyte, making batteries much safer and more stable. But there’s a challenge—solid electrolytes are difficult and expensive to produce.
In 2021, Dr. Ha’s team developed an innovative “coprecipitation method,” which allows solid electrolytes to be made in a single-step process.
This technique removes the need for expensive lithium sulfide (Li₂S) and eliminates complex milling and evaporation steps, significantly lowering costs. Their research attracted major attention, and the technology was transferred to a Korean company, Daejoo Electronic Materials Co., Ltd., for industrial use.
Since then, KERI has worked with top institutions, including KAIST and POSTECH, to further refine the process.
Their latest breakthrough—the “enhanced coprecipitation method”—has made production even faster and improved the quality of solid electrolytes.
The key to the improved method is how the raw materials dissolve and precipitate in a solution. The researchers found an optimal way to mix lithium, sulfur, and a catalyst, ensuring the correct formation of lithium polysulfides and lithium sulfide.
By applying this knowledge, they developed a technique for producing different types of solid electrolytes, such as Li₃PS₄ and Li₆PS₅Cl, more efficiently.
With support from KAIST researchers, who analyzed the chemical changes during lithium dissolution, and experts at POSTECH, who used quantum calculations and mass spectrometry to study molecular structures, the team was able to optimize the process. This allowed Daejoo Electronic Materials to adapt the method for real-world manufacturing.
Thanks to the upgraded method, the production time for solid electrolytes has been cut from 14 hours to just 4 hours. The quality has also improved—previous methods faced problems with lower ion conductivity when scaled up, but this new approach achieves an impressive conductivity of 5.7 mS/cm, exceeding the levels of traditional liquid electrolytes (around 4 mS/cm).
When tested in a 700mAh all-solid-state battery pouch cell (about 1/5 the size of a smartphone battery), the energy density reached 352Wh/kg—higher than that of commercial lithium-ion batteries (270Wh/kg). Even after 1,000 charge-discharge cycles, the battery retained over 80% of its capacity, proving its long lifespan.
The findings, published in the journal Energy Storage Materials, show that this technology could revolutionize not just battery production but also other areas like functional coatings. A patent has been filed, and the research team is optimistic that their work will make mass production of ASSBs more practical and affordable.
Dr. Ha Yoon-Cheol emphasized the importance of this achievement, stating, “Our previous work was groundbreaking in introducing coprecipitation technology for solid electrolytes. Now, with this enhanced version, we have fine-tuned the process to deliver even better results. This breakthrough will help make large-scale production of ASSBs a reality at a lower cost.”
With this development, we may soon see safer, longer-lasting, and more energy-efficient batteries powering our everyday devices, electric vehicles, and even renewable energy storage systems.
Source: KSR.