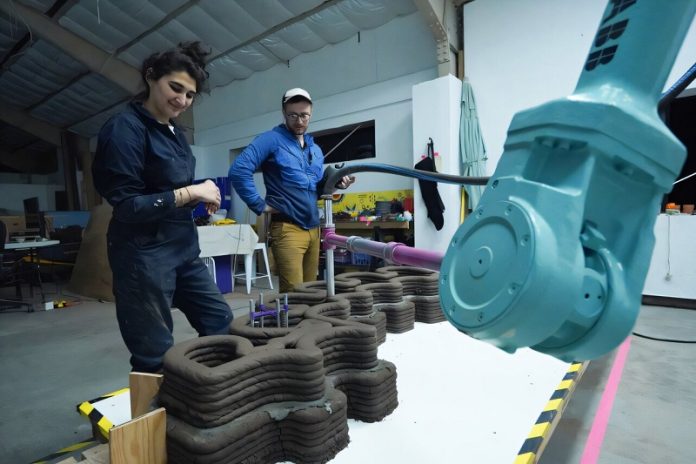
Construction costs are rising, but researchers at MIT have found a way to make building with concrete cheaper and more environmentally friendly—by using mud.
They’ve developed a method called EarthWorks, which turns soil, including dirt from construction sites, into molds for concrete structures.
This innovative approach uses 3D printing to replace the traditional and expensive wooden molds used in construction.
Sandy Curth, a Ph.D. candidate at MIT and the leader of the project, explains, “We’ve shown that we can take the ground we’re standing on or leftover soil from a construction site and turn it into precise, flexible molds for custom concrete designs.”
When concrete structures are built, wooden molds called formworks are first constructed to shape the concrete.
This process is expensive, time-consuming, and wasteful. The EarthWorks method replaces these wooden molds with soil-based ones.
With the help of 3D printing, soil is shaped into reusable molds that can handle wet concrete just as well as wood.
The soil is mixed with additives like straw and coated with a wax-like material to prevent water from leaking out of the concrete. Once the concrete sets, the soil mold can be broken down and recycled for future use.
“It’s just dirt, and it’s infinitely reusable,” Curth says.
This technique doesn’t require drastic changes to how buildings are constructed, making it easier for the construction industry to adopt. Builders would need a large 3D printer on-site, but they could save significantly on material costs.
Concrete production is responsible for about 8% of global carbon emissions. The EarthWorks method can reduce emissions in two ways.
First, soil-based molds are less resource-intensive than wood. Second, the technique allows for shape-optimized concrete designs, which use less material without sacrificing strength.
Previous research by Curth’s team showed that optimizing concrete shapes could cut carbon emissions from structural frames by over 50%. “This method brings advanced, low-carbon designs closer to reality,” says Caitlin Mueller, an MIT professor and co-author of the study.
By using soil molds, architects and engineers can create complex, custom concrete designs as easily as they would make standard rectangular ones. “We can make advanced, efficient shapes in the same time and energy it takes to build simple ones,” Curth adds.
The EarthWorks project is highly collaborative, involving multiple researchers from MIT and beyond. Curth credits his advisors, Professors Lawrence Sass and Caitlin Mueller, for their roles in advancing computational design and innovative structural methods.
The team’s latest study, published in Construction and Building Materials, details their progress.
Curth has also founded FORMA Systems, a company aimed at bringing EarthWorks into the construction industry. Looking ahead, he hopes the method could go beyond concrete molds to produce entire buildings made from soil. While adobe homes already exist in some parts of the world, this approach could modernize and systematize their production, making them cheaper and more accessible.
“People have built with mud for thousands of years,” Curth says. “This approach updates that tradition to meet modern demands, creating high-performance, low-cost buildings that are better for the planet.”