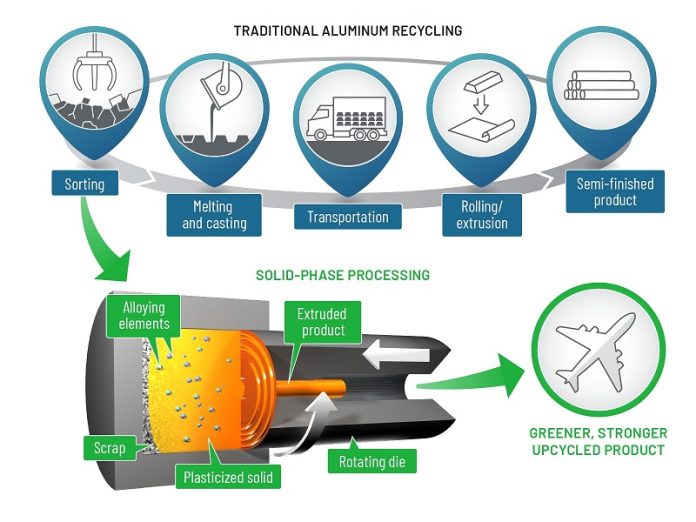
A groundbreaking method developed by researchers at the Department of Energy’s Pacific Northwest National Laboratory (PNNL) offers a way to turn scrap aluminum into high-performance alloys without traditional melting processes.
This innovation, called solid phase alloying, provides a faster, cheaper, and more sustainable way to recycle industrial aluminum waste into valuable materials.
The research, published in Nature Communications, shows that the recycled aluminum performs just as well as newly produced aluminum, offering a promising alternative to conventional manufacturing.
This could lower costs and reduce the environmental impact of producing high-quality aluminum products.
Using solid phase alloying, scrap aluminum is mixed with metals like copper, zinc, and magnesium to create strong, durable alloys in just a single step.
The process is incredibly fast, taking less than five minutes to achieve results that would typically require several days with traditional methods such as melting, casting, and extrusion.
“The novelty of our work is that we transform low-cost waste into high-cost products,” said Xiao Li, a PNNL materials scientist and lead author of the study. “This is done in a single step, saving both time and energy.”
The team used a patented technique called Shear Assisted Processing and Extrusion (ShAPE) to accomplish this.
In the ShAPE process, a high-speed rotating die generates friction and heat to blend the materials evenly, creating a uniform alloy with properties similar to newly manufactured aluminum.
One of the biggest advantages of this method is its ability to eliminate energy-intensive bulk melting.
This not only saves energy but also makes use of low-cost scrap materials. For consumers, it means recycled aluminum products could last longer, perform better, and cost less. Applications include vehicles, construction materials, and household appliances.
The research also revealed that this process produces unique atomic-scale structures in the aluminum. Known as Guinier-Preston zones, these features significantly improve the strength of the alloy.
Compared to conventional recycled aluminum, the upcycled version is 200% stronger and has higher tensile strength, leading to more durable and reliable products.
While the current focus is on aluminum, researchers believe this method could be applied to a wide range of metals. “Solid phase alloying could work with virtually any metal combination,” said Cindy Powell, PNNL’s chief science and technology officer. “It opens the door to creating entirely new alloys that weren’t possible before.”
This technique could also benefit advanced manufacturing technologies like 3D printing. Wire arc additive manufacturing (WAAM), which uses metal wires to 3D print or repair parts, often requires customized materials. Solid phase alloying provides a simple way to create these tailored alloys with precise compositions, such as 2% or 5% copper.
By transforming industrial waste into high-value materials, solid phase alloying offers a sustainable solution to meet growing demand for high-performance metals.
This innovative method has the potential to revolutionize recycling and manufacturing, making strong, long-lasting materials more affordable and environmentally friendly.