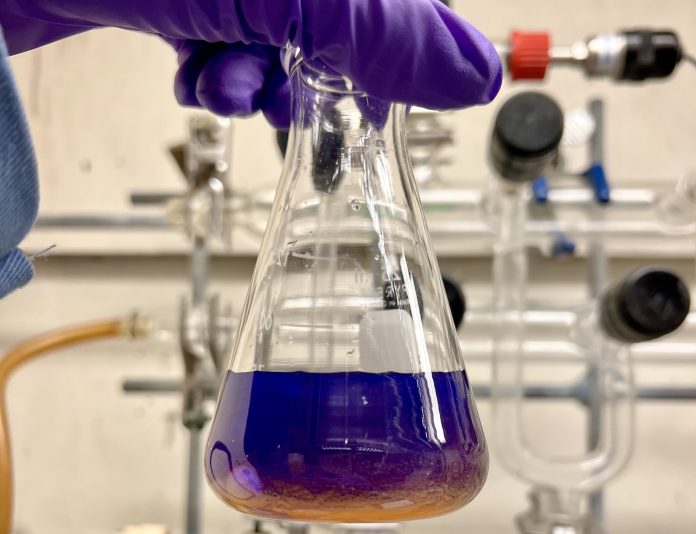
Cobalt is a vital material in lithium-ion batteries, powering everything from smartphones to electric cars.
But how it’s sourced often raises ethical and environmental concerns.
Around 70% of the world’s cobalt comes from the Democratic Republic of Congo, where mining can harm ecosystems, pollute water, and put workers at risk.
Additionally, with demand for batteries growing, a global cobalt shortage could disrupt supply chains.
To address these challenges, researchers at the University of Pennsylvania have developed a cleaner, more sustainable way to separate cobalt from nickel, another critical battery metal.
Their new method uses a simpler and less harmful process to extract these metals from waste materials, potentially reducing the need for harmful mining practices.
The findings, published in the journal Chem, could pave the way for a greener approach to producing purified cobalt.
“Our method is simpler, cheaper, and better for the environment,” said Eric Schelter, lead researcher and professor of chemistry at Penn.
“It also creates value from discarded batteries by efficiently separating cobalt and nickel.”
A smarter way to separate metals
Traditionally, cobalt is extracted as a byproduct of nickel mining through energy-intensive methods like acid leaching and solvent extraction. These processes use strong chemicals that produce hazardous waste and harm the environment.
Schelter’s team developed a different approach based on the unique chemical properties of cobalt and nickel. They discovered that by using ammonia and a negatively charged molecule (called an anion), they could cause cobalt to form a solid structure and separate from nickel. This process relies on the cobalt and nickel complexes bonding differently with the ammonia, allowing the researchers to selectively precipitate cobalt while leaving nickel in solution.
“This process achieves purities of 99.4% for cobalt and over 99% for nickel,” said Boyang “Bobby” Zhang, the study’s first author. “It avoids using harsh acids and solvents, making it safer and better for the environment.”
The team also evaluated the real-world impact of their method. They found that it significantly reduces environmental risks compared to traditional methods. By eliminating harmful organic solvents, the process cuts greenhouse gas emissions and hazardous waste, improving metrics like air quality and human health impacts.
Economically, the method is also competitive. The team estimated that producing purified cobalt with this process costs $1.05 per gram, much lower than the $2.73 per gram in other methods.
“We focused on using affordable and widely available chemicals, which makes this method both cost-effective and scalable,” Schelter said.
A step toward sustainable metal recovery
This new approach could transform how critical metals are recovered, reducing the environmental impact of battery production.
The principles behind the process may also be applied to other metals, helping drive broader innovation in sustainable chemistry.
“This is just the beginning,” said Schelter. “We’re excited to explore how this method can be expanded to solve other metal separation challenges, creating cleaner technologies for a more sustainable future.”
Source: University of Pennsylvania.