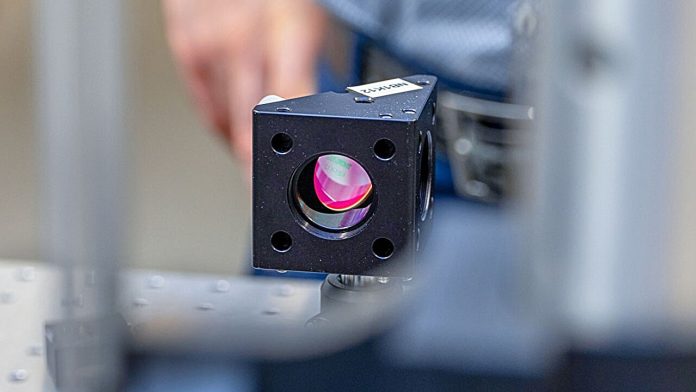
In a new discovery, researchers from Cornell University have found how tiny metal particles, when launched at supersonic speeds, can bond tightly with a metal surface.
This type of bonding, known as “solid-state bonding,” happens without melting the metal.
The findings could help improve 3D printing and other manufacturing methods that rely on high-speed metal bonding.
The researchers used a custom-built machine that launches micrometer-sized aluminum particles at more than 2,200 miles per hour toward a metal surface, called a substrate.
This extreme speed allows the particles to create atomic-level bonds with the substrate on impact.
Solid-state bonding like this can create strong, long-lasting connections between metals, making it useful for creating and repairing metal surfaces, especially in fields like aerospace and energy where durability is key.
This bonding process is also central to “cold spray” 3D printing, a type of 3D printing that builds materials without heating or melting them. Cold spray methods create parts with excellent mechanical strength, which makes them suitable for building and repairing strong structural components in demanding industries.
The study, published in Nature Communications, offers a closer look at how these bonds form on a tiny scale.
The researchers used high-precision tools, including a scanning electron microscope, to measure bond strength at various points along the impact surface.
Interestingly, they found that the bond strength wasn’t the same across the entire impact area.
In fact, the bond was weakest at the center of the impact, while strength increased sharply moving outward, eventually leveling off near the edges.
One of the surprising findings was how the presence of a thin oxide layer—formed naturally on the metal’s surface—affects the bonding strength.
When the oxide layer broke into tiny pieces during the impact, the bond became stronger. In contrast, regions where the oxide layer stayed mostly intact showed weaker bonds.
This is because the impact fractures the oxide layer, allowing more of the underlying metal to contact the substrate directly, creating a stronger bond.
To explain this variation, the researchers created a model that takes into account two key factors: the pressure of the impact and how much metal surface is exposed.
When a tiny particle hits the substrate at supersonic speed, the force causes the oxide layer to break, exposing fresh metal. At the same time, the pressure from the impact brings the exposed metals close enough to form a strong atomic bond.
This discovery could help scientists and engineers design stronger and more precise bonding methods.
By controlling factors like particle size, speed, and material choice, they can create stronger bonds for applications in industries that require durable materials. It might even help protect sensitive equipment, like spacecraft or telescopes, from bonding with unwanted particles in space.
Overall, these insights offer new possibilities for designing stronger materials and could improve technology in fields ranging from advanced manufacturing to space exploration.