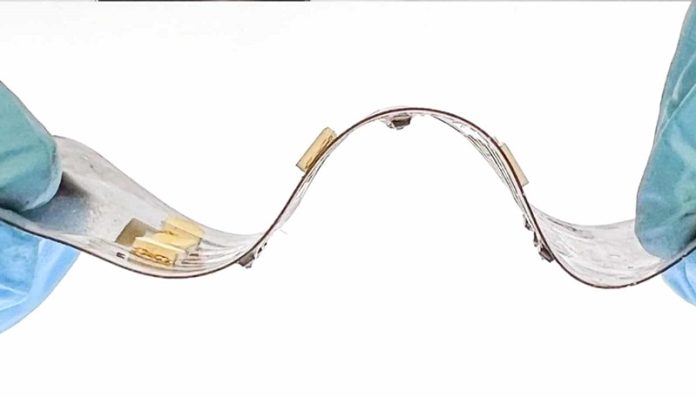
Imagine if your phone could bend or twist without breaking, or if hospital equipment were soft and comfortable for patients to wear.
This may sound like science fiction, but a team of researchers has developed a new way to make flexible electronics that could someday lead to these possibilities.
Led by Michael Bartlett, an associate professor of mechanical engineering at Virginia Tech, the research focuses on creating circuits that can bend and stretch but still work as well as traditional electronics.
Published in Nature Electronics, the team’s method could make advanced devices for soft robotics and wearable technology.
Traditional circuit boards are rigid, with electric connections created by drilling tiny holes through hard layers.
But for flexible materials, like those needed for wearable tech or soft robots, these hard connections don’t work well.
Bartlett’s team found a way to solve this by using liquid metal microdroplets to make soft, bendable connections across circuit layers.
“These soft connections, called vias, let us create flexible electronics that can twist, bend, and stretch,” says Bartlett. “This opens doors for developing new types of gadgets and health devices that are durable and comfortable.”
The process is quite innovative. Instead of drilling holes, Bartlett’s team uses liquid metal droplets that settle in a stair-step pattern, forming small connections within the material.
These droplets create electric pathways that connect different layers of a soft circuit without any drilling, allowing electricity to flow smoothly across the layers.
Here’s how it works: the liquid metal droplets are placed within a material called photoresin. When exposed to ultraviolet (UV) light, the resin causes the droplets to align in a controlled pattern that looks like a staircase.
This 3D alignment makes it easy for the droplets to connect the top and bottom layers of the circuit.
The entire process is very quick, taking under a minute to make multiple connections at once. Once the droplets are set in place, the resin is fully cured, “locking in” the structure so it can handle bending and stretching.
Dong Hae Ho, a postdoctoral researcher working with Bartlett, explains, “We used effects that are usually unwanted in standard manufacturing to our advantage. The result is a soft, conductive connection that maintains flexibility and strength.”
This new method allows multiple layers of flexible electronics to connect seamlessly, making it possible to create complex circuits for a range of soft devices. These liquid metal vias and interconnects can be repeated across many layers, building intricate, multilayered circuits in a flexible material.
Bartlett’s research, supported by grants from the Office of Naval Research and the National Science Foundation, is an exciting step toward flexible electronics.
In the future, this technology could lead to a wide range of applications, from wearable health monitors to soft robots that can squeeze into tight spaces, all while staying durable and comfortable for users.