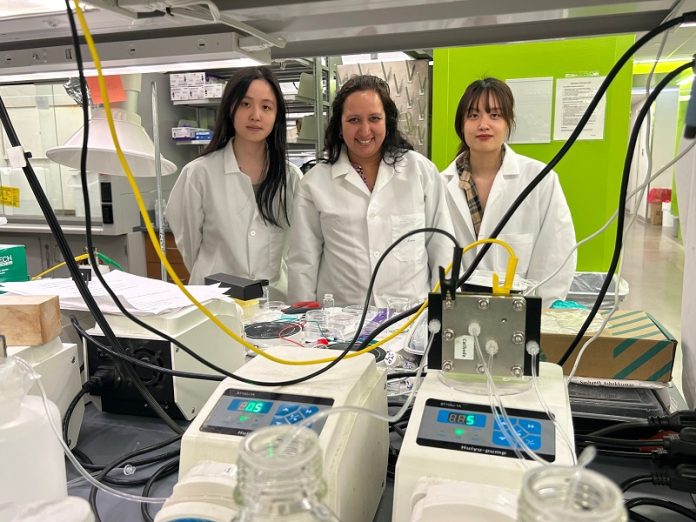
A team of engineers at Rice University has developed a groundbreaking reactor that efficiently extracts lithium from natural brine—salty water found in geothermal sources.
This invention could help meet the rising demand for lithium, which is essential for making batteries used in electric vehicles and renewable energy storage.
Traditional methods for lithium extraction are challenging due to high energy use and the difficulty of separating lithium from other similar elements.
But this new reactor promises a more efficient and environmentally friendly way to obtain high-purity lithium.
Natural brines are an appealing lithium source as traditional mining becomes harder and more expensive.
However, these brines also contain other ions like sodium, potassium, magnesium, and calcium, which share similar chemical properties with lithium.
Separating lithium from these ions has been difficult and energy-intensive, leading to high costs and environmental issues, including the production of hazardous chlorine gas in conventional processes.
The Rice University team, led by professors Lisa Biswal and Haotian Wang, designed a novel three-chamber electrochemical reactor to overcome these challenges.
This reactor’s design includes a middle chamber with a special porous electrolyte that allows ions to pass through while blocking harmful reactions.
The middle chamber prevents chlorine gas formation by blocking chloride ions from reaching areas where they could react and produce this dangerous by-product.
The real breakthrough lies in a specialized membrane called LICGC (lithium-ion conductive glass ceramic) on one side of the reactor.
This membrane selectively allows only lithium ions to pass through, while blocking other ions like potassium, magnesium, and calcium. LICGC membranes are typically used in solid-state batteries, but the Rice team found they could also serve a unique purpose in lithium extraction.
By using this technology, the reactor achieved an impressive lithium purity rate of 97.5%, making it highly effective in separating lithium from other elements.
This is crucial for producing high-quality lithium hydroxide, an important material in battery production. Moreover, the reactor minimized the production of chlorine gas, making the process much safer and reducing its environmental impact.
While testing, the team discovered a minor issue with the reactor’s long-term stability. Sodium ions tended to accumulate on the LICGC membrane over time, which could slow down lithium extraction and increase energy consumption.
However, the researchers are exploring solutions like using lower current levels, adding surface coatings, or pulsing the current to prevent this buildup and enhance the reactor’s efficiency.
This new reactor represents a major step forward in sustainable lithium extraction from geothermal brines.
With further development, it could ensure a steady supply of lithium for the growing demand in renewable energy and electric vehicles, offering a cleaner and more efficient alternative to traditional extraction methods.
“Our goal was to make lithium extraction more efficient and eco-friendly,” said Wang, an associate professor of chemical and biomolecular engineering at Rice. “This reactor shows what’s possible when scientific principles are combined with engineering creativity to address real-world challenges.”