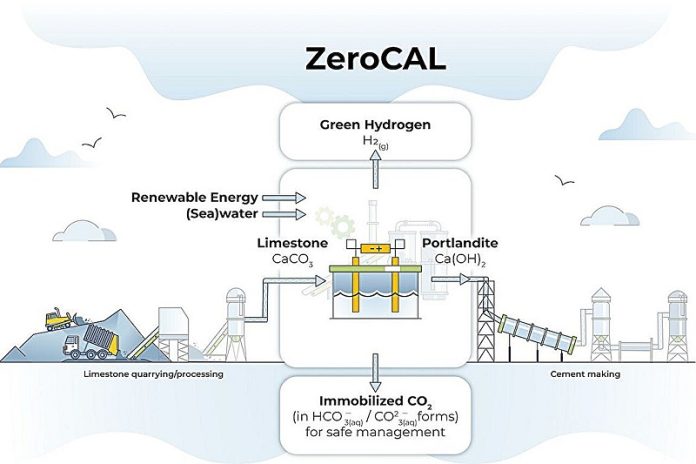
Cement production is responsible for nearly 8% of global carbon dioxide (CO2) emissions, but researchers at UCLA’s Institute for Carbon Management (ICM) have developed a new method that could dramatically reduce this environmental impact.
Their solution, called “ZeroCAL,” could remove nearly all of the CO2 emissions produced during cement manufacturing.
This approach was recently detailed in a study published in ACS Sustainable Chemistry & Engineering.
Cement, especially Ordinary Portland Cement, is used worldwide as the main binding material in concrete, the second most-used material on Earth after water.
The process of making cement involves heating limestone, which results in significant CO2 emissions.
Around 60% of these emissions come from the chemical breakdown of limestone, while the other 40% comes from burning fossil fuels to heat the kilns.
On average, for every kilogram of cement produced, nearly one kilogram of CO2 is released.
The energy required for this process is also high, with one metric ton of lime (the material that becomes cement) needing about 1.4 megawatt hours of energy, enough to power a home for a month.
The UCLA researchers, led by Gaurav Sant, developed a new method that could drastically cut CO2 emissions from cement production.
Instead of using limestone directly, their method dissolves it in a water-based solution with a common industrial acid.
This process separates the calcium from the limestone, and then an electrochemical process is used to create calcium hydroxide, a zero-carbon precursor for lime production. When heated, calcium hydroxide releases only water, not CO2.
The researchers estimate that their method, called ZeroCAL (short for zero carbon lime), could eliminate up to 98% of the CO2 emissions linked to traditional cement production.
An added benefit of this method is that it produces useful byproducts like hydrochloric acid, baking soda, oxygen, and hydrogen gas. The hydrogen can even be used as a clean fuel to heat the cement kilns, further reducing emissions.
Although the ZeroCAL method currently uses more energy than conventional processes, the team believes it can achieve energy efficiency through further improvements. They suggest focusing on cement plants near coasts or rivers, where water is easily accessible, to meet the process’s water needs.
The team is already collaborating with Ultratech Cement Limited, India’s largest cement manufacturer, to build a demonstration plant that will produce one metric ton of lime per day using the ZeroCAL process.
Beyond cement, the researchers believe their carbon-free lime could also help decarbonize steel production, offering a pathway to make multiple industries more sustainable.
As study co-author Fabian Rosner explained, “The ZeroCAL process offers a unique, scalable solution to help decarbonize cement production—an urgent step needed to combat climate change.”
Source: UCLA.