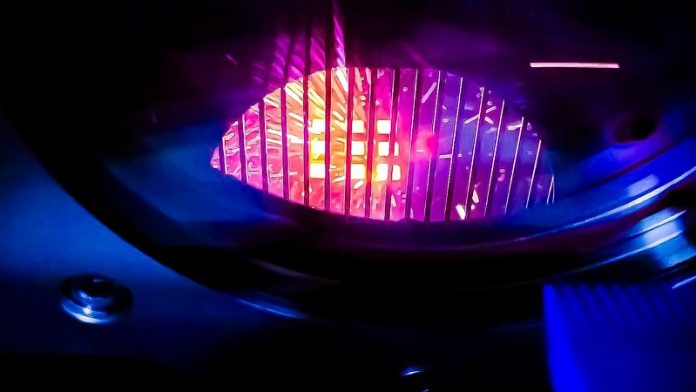
Researchers at Oak Ridge National Laboratory (ORNL) and the National Energy Technology Laboratory have developed and 3D printed a new lightweight metal alloy that can withstand extremely high temperatures—above 2,400 degrees Fahrenheit—without melting.
This is a major breakthrough for industries that use gas turbines, such as airplanes, as it could lead to more efficient engines that produce less carbon emissions.
The key to this new material is its unique composition.
The researchers combined seven different elements in a niobium-rich alloy, which can withstand heat far better than traditional metals used in turbine engines.
In fact, the melting point of this new alloy is at least 48% higher than nickel and cobalt-based superalloys previously developed by ORNL.
This higher melting point means the new alloy can handle the extreme heat produced in gas turbines without breaking down.
What makes this achievement even more exciting is that the researchers used a special 3D printing process called electron beam melting to create parts from the new alloy.
This method allowed them to fine-tune the process and avoid cracks, which is a common issue when working with high-temperature metals.
“No one has been able to create and 3D print alloys with such a high melting point and low weight without cracks before,” said Saket Thapliyal from ORNL. He explained that while metals like tungsten can also withstand very high temperatures, they are too heavy to use in airplanes.
This new alloy, however, is lightweight and still maintains its strength at ultra-high temperatures, making it ideal for applications like turbine blades in jet engines.
This breakthrough could lead to the creation of turbine engines that are lighter, more efficient, and produce fewer carbon emissions, contributing to a cleaner and more sustainable future for the aviation industry.