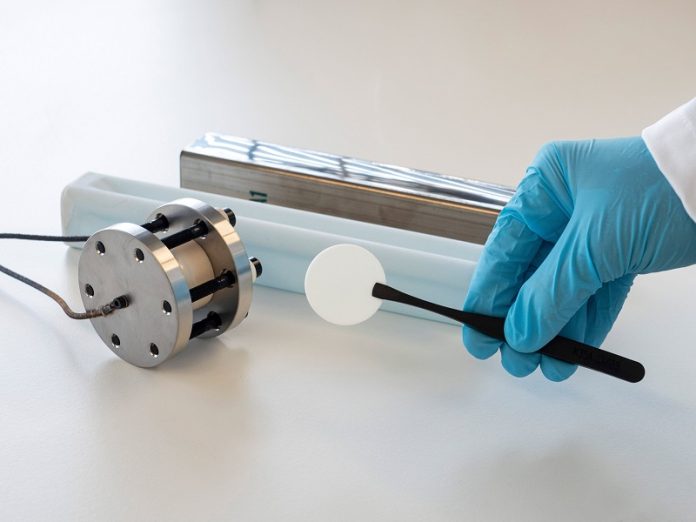
In 1997, the Mercedes-Benz A-Class famously tipped over during the “elk test.”
One reason for the incident was a design change: the car was initially meant to be electric, using a heavy salt battery.
Switching to a lighter combustion engine battery shifted the car’s center of gravity, leading to the tip-over.
Salt batteries work differently than most other batteries. Instead of using a liquid electrolyte, they use a solid ceramic electrolyte made from sodium aluminum oxide, also called beta-alumina.
This makes salt batteries non-flammable and safer, as they can’t burn or explode.
The battery’s cathode is made of common salt and nickel powder, while the anode, made of sodium metal, forms only during charging.
While salt batteries didn’t prove ideal for electric vehicles (which now run mostly on lithium-ion batteries), they are still being studied for other uses.
In 2016, Empa, a Swiss research institution, teamed up with HORIEN Salt Battery Solutions to improve these batteries as part of a government-supported project.
The focus has been on improving the ceramic electrolyte and optimizing the battery’s overall structure.
Salt batteries need a high operating temperature of around 300°C, but this makes them less sensitive to temperature changes compared to lithium-ion batteries.
This feature is especially beneficial in locations with harsh conditions, like mining sites, tunnels, and offshore platforms, where lithium-ion batteries are not allowed due to fire risks.
Despite the high temperatures, salt batteries can be more efficient in specific situations. According to researcher Meike Heinz from Empa, it’s easier to keep a battery warm than to cool it down. This is because the battery generates heat during charging and discharging, allowing it to maintain its operating temperature.
Salt batteries are ideal for applications like emergency power storage in critical infrastructure, such as mobile phone towers. They are long-lasting and maintenance-free, making them a reliable option in remote areas.
Empa researchers are also working on making salt batteries more sustainable and cost-effective. Most of the raw materials used in these batteries are inexpensive and easy to recycle. However, nickel, a critical component of the battery’s cathode, is becoming more difficult to source. To address this, Empa and HORIEN are exploring ways to reduce or replace nickel with other materials, such as zinc.
One ongoing EU project, SOLSTICE, aims to replace nickel entirely with zinc in salt batteries. Although zinc’s low melting point is a challenge at high temperatures, researchers are finding promising ways to stabilize the battery’s structure.
Future projects are being planned to further improve and scale up these nickel-free salt batteries. The goal is to produce affordable, safe, and long-lasting salt batteries that could be used not just for small applications but to power entire residential areas.
With their safety, durability, and use of abundant materials, salt batteries could become a key solution for sustainable and reliable energy storage.
Source: KSR.