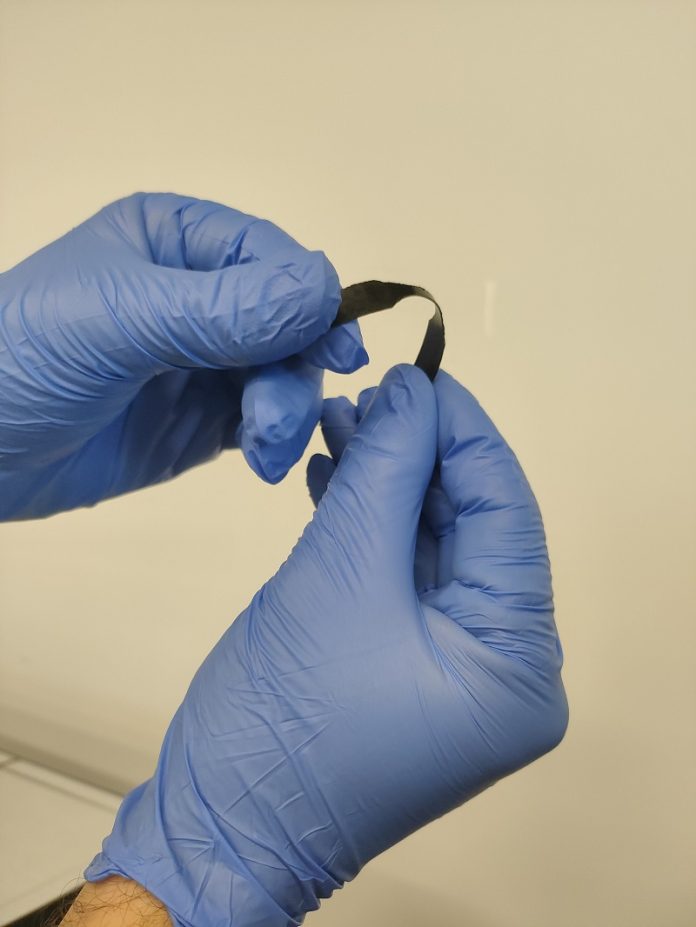
Scientists have found a new way to make recyclable plastics much stronger by using carbon nanotube derivatives.
Plastics have a big environmental impact, and making them more durable and easier to recycle is one way to help reduce this problem.
Generally, there are two main types of plastics: thermoplastics and thermosets.
Thermoplastics can be melted and reshaped, but their quality decreases after several melts.
Thermosets, on the other hand, don’t melt at high temperatures because their molecular chains are strongly bonded together, but they can’t be recycled easily.
Thermoset plastics, like epoxy resin and silicone, are stronger than thermoplastics and are commonly used in construction.
However, they are also more brittle. To make them stronger, engineers usually add materials like carbon fibers, which are already used to make durable products such as sports equipment and helmets. The downside is that these reinforced plastics can’t be recycled easily.
Researchers at IMDEA Nanociencia, led by Emilio Pérez, have developed a strategy to strengthen recyclable plastics while keeping them reusable.
They’re working with a type of plastic called a “covalent adaptable network,” which is similar to thermoset plastics but has reversible bonds. This means that while the bonds between the polymer chains are strong, they can still be broken and reformed.
The team’s innovation involves using carbon nanotubes with a special ring-like molecule around them, called MINTs.
This ring is attached to the nanotube in a way that keeps it very strong but allows some movement along the tube. The researchers designed the ring with two bonding points that connect to the plastic polymer.
This way, the nanotube becomes part of the plastic’s structure.
Carbon nanotubes are like rolled-up sheets of graphene, a super-strong material. Normally, attaching molecules to nanotubes weakens them. But by using a mechanical bond (the ring), the researchers avoid damaging the nanotube, preserving its strength.
This technique improves the plastic’s mechanical strength dramatically. Even with only 1% of nanotubes added by weight, the plastic’s Young’s modulus, a measure of stiffness, improves by 77%, and its tensile strength doubles.
Remarkably, these properties remain unchanged even after the plastic is melted and recycled four times.
The researchers say this efficient transfer of mechanical stress between the polymer and the nanotube is key to making the material stronger. Adding more nanotubes doesn’t help because they tend to clump together, reducing their effectiveness.
This discovery could lead to lighter, stronger, and recyclable materials for use in industries like car and airplane manufacturing, resulting in significant fuel savings and a more sustainable future.