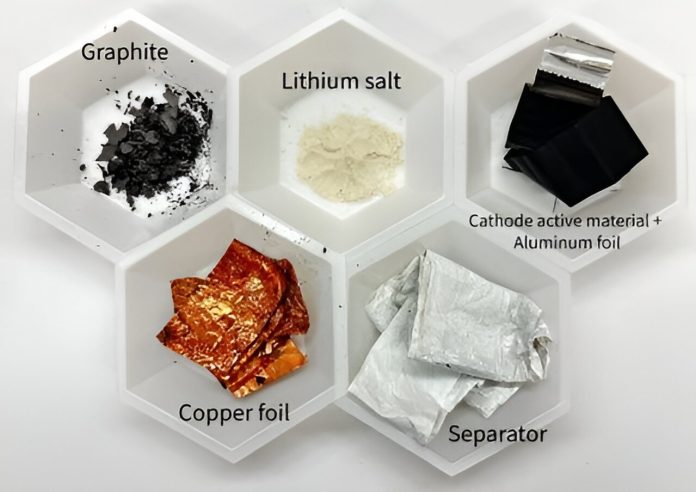
Lithium-ion batteries are everywhere—in our phones, laptops, electric vehicles, and even our children’s toys.
These batteries have become an essential part of our daily lives because they store energy efficiently.
However, the element that makes these batteries so powerful, lithium, is in high demand and is considered a critical material by the U.S. Department of Energy.
This high demand, along with the risk of supply shortages, makes it crucial to find better ways to recycle and reuse lithium.
Surprisingly, only about 5% of lithium batteries are currently being recycled.
This is a missed opportunity because discarded batteries could be a valuable source for recovering lithium.
As a result, scientists are working hard to develop better and more efficient ways to recycle lithium from old batteries.
Most current recycling methods involve using harsh chemicals or high heat to break down the batteries and extract the lithium.
While these methods can be effective, they also produce toxic byproducts and require a lot of energy, making them less environmentally friendly.
But now, scientists at the U.S. Department of Energy’s Ames National Laboratory have developed an innovative new process that could change the way we recycle lithium-ion batteries.
This process, known as the Battery Recycling and Water Splitting (BRAWS) technology, uses only water and carbon dioxide (CO2) to recover lithium. What makes this method so exciting is that it doesn’t require any chemicals or extreme heat, making it much more environmentally friendly.
Dr. Ikenna Nlebedim, a scientist at Ames Lab and the leader of the research team, explains that there are currently three main methods for recycling lithium-ion batteries: hydrometallurgical, pyrometallurgical, and direct recycling.
Hydrometallurgical recycling involves grinding up old batteries and dissolving the materials in acid.
The recyclable elements are then extracted using different chemicals. Pyrometallurgical recycling uses high temperatures to melt the waste, allowing the recyclable materials to be separated and collected.
Direct recycling, on the other hand, involves physically taking apart the battery to collect reusable materials.
Each of these methods has its pros and cons, but they all come with some drawbacks. The BRAWS technology, however, combines the best features of these methods while avoiding their disadvantages.
One of the biggest challenges with lithium-ion batteries is that fast charging can cause lithium to build up on the anode, the positive side of the battery. Over time, this buildup can cause the battery to fail.
The BRAWS process takes advantage of this by using fast charging to force as much extra lithium as possible onto the anode.
After this step, the battery is carefully taken apart. In the lab, this dismantling is currently done by hand. The anode, usually made of graphite, is then placed in water, and CO2 is added. This reaction causes the lithium to be recovered as lithium carbonate, a valuable material that can be reused.
What’s even more remarkable is that this process also produces green hydrogen as a byproduct. Because lithium is highly reactive, when the anode is placed in water, it splits the water molecules, releasing hydrogen gas, which can be captured and used as a clean fuel.
At the same time, the CO2 used in the process is absorbed, helping to reduce its presence in the environment.
This new method not only recycles lithium more efficiently but also has the potential to be more profitable. By recovering lithium, extracting other reusable parts of the battery, and producing green hydrogen all at once, the BRAWS technology strengthens the economic viability of recycling lithium-ion batteries.
Dr. Nlebedim believes that recycling needs to be economically sustainable to be widely adopted.
With this new technology, the team at Ames National Laboratory is paving the way for a greener and more efficient future in battery recycling, making it easier to reuse valuable materials while also benefiting the environment.
Source: Ames National Laboratory.