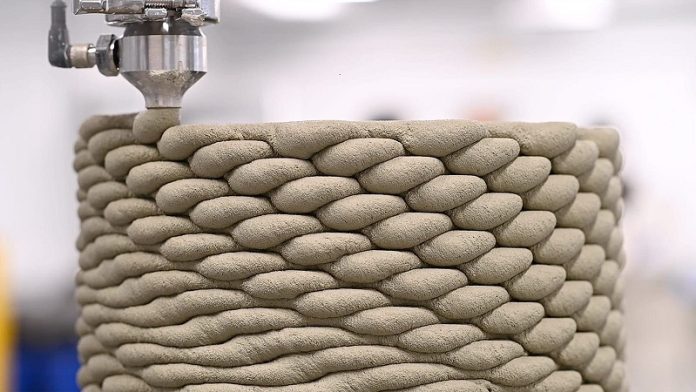
Researchers from Princeton University have developed a new way to make concrete more resistant to cracking by drawing inspiration from nature.
By combining advanced design techniques with robotic manufacturing, they improved crack resistance by as much as 63% compared to traditional concrete.
Their findings, led by Reza Moini, assistant professor of civil and environmental engineering at Princeton, were recently published in Nature Communications.
The researchers found inspiration in the double-helix structures of the coelacanth, an ancient fish species.
These fish scales have unique structural patterns that make them strong and crack-resistant.
Moini’s team used this natural design to guide their work, demonstrating how architecture can improve material properties like strength and fracture resistance.
To create their improved concrete, the researchers used robotic technology to build concrete in layers, creating strands arranged in a 3D design. These strands were weakly connected, allowing them to work together to resist cracking.
They further enhanced the design by twisting the strands into a double-helical arrangement, similar to the coelacanth’s scales, which strengthened the concrete and made it better at resisting crack propagation.
The new design includes what researchers call a “toughening mechanism.” This involves several strategies to prevent cracks from spreading through the material. For example, cracks are deflected or the fractured surfaces are interlocked, making it harder for cracks to move in a straight path.
One of the challenges in creating such complex designs is that they require precision, which is difficult to achieve using traditional methods. That’s where robots come in. Robotic additive manufacturing (also known as 3D printing) allows for precise placement of concrete, building structures layer by layer. Shashank Gupta, a graduate student and co-author of the study, explained that robots are key to creating these intricate designs on a large scale, especially for structures like beams and columns.
In Moini’s lab, researchers used large industrial robots to integrate real-time processing and create full-sized concrete components. These structures were not only stronger but also aesthetically pleasing.
A major issue the team had to overcome was concrete’s tendency to deform under its weight while being built. When fresh concrete is deposited, the weight of the upper layers can cause the lower layers to deform. To solve this problem, the researchers developed a system that controls how fast the concrete hardens.
They used a two-part system at the robot’s nozzle, where one inlet dispensed concrete and the other a chemical accelerator. This allowed the concrete to harden quickly and maintain its shape, even under the weight of the structure.
By using these innovative techniques, the researchers were able to build complex and strong concrete structures that are less likely to crack, opening the door for more durable and creative designs in construction.
Source: Princeton University.