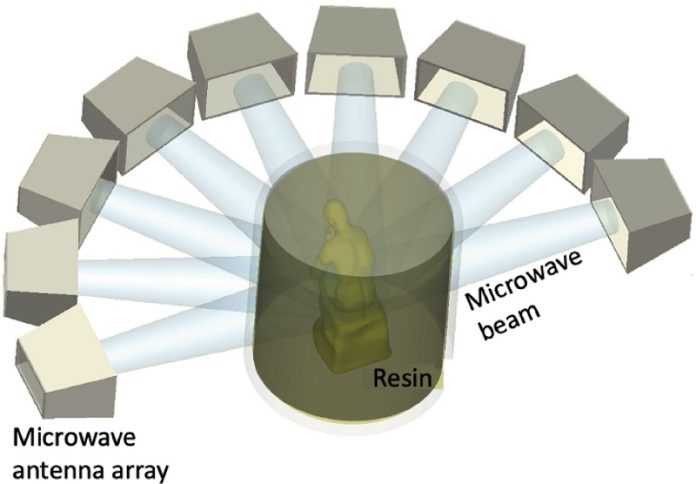
In the fast-changing world of 3D printing, researchers are always looking for ways to make the process faster and more versatile.
A team from Lawrence Livermore National Laboratory (LLNL) has developed a new technique called Microwave Volumetric Additive Manufacturing (MVAM), which uses microwave energy to create 3D-printed parts.
This method could unlock new possibilities for 3D printing, allowing for the use of a wider range of materials.
In traditional 3D printing, light-based methods are often used to cure (harden) materials.
However, these methods are limited because they work best with transparent materials, making it difficult to print with opaque or composite materials.
The new microwave approach, described in a study published in Additive Manufacturing Letters, solves this issue by allowing microwaves to penetrate deeper into materials.
This breakthrough means that materials like opaque resins can now be used, expanding the possibilities of 3D printing.
Saptarshi Mukherjee, one of the lead researchers at LLNL, believes this new technique could change the way we think about 3D printing.
“This could revolutionize additive manufacturing,” Mukherjee said. “We could now print large, complex parts quickly using microwaves.”
Microwave energy can cure materials more efficiently than light. The researchers developed a model to simulate how microwaves interact with different materials, allowing them to fine-tune the curing process.
In experiments, they found that while existing microwave hardware could cure resins in about 2.5 minutes, increasing the power could reduce curing times to just six seconds. This would speed up 3D printing and allow for the creation of much larger parts, even up to meter-sized structures.
This new approach has many potential applications. The ability to use a broader range of materials, including opaque and composite materials, could lead to the development of stronger, more heat-resistant, and conductive parts.
This is particularly promising for industries like aerospace, automotive, and healthcare, where complex, high-performance parts are essential.
Johanna Schwartz, the team’s chemistry lead, said this technique opens up new possibilities for 3D printing. “With microwave VAM, we can now explore materials that weren’t possible to print with light-based systems,” she said.
The team is working to improve the MVAM system, and they are hopeful that this technology will make 3D printing more efficient and versatile. However, they acknowledge that the high cost of microwave systems is a challenge. To make the process more affordable, the researchers are exploring ways to custom-build parts of the system themselves.
As they continue refining the process, the team believes their work could push the boundaries of what’s possible in 3D printing, creating new opportunities for manufacturers across various industries.
Source: Lawrence Livermore National Laboratory.