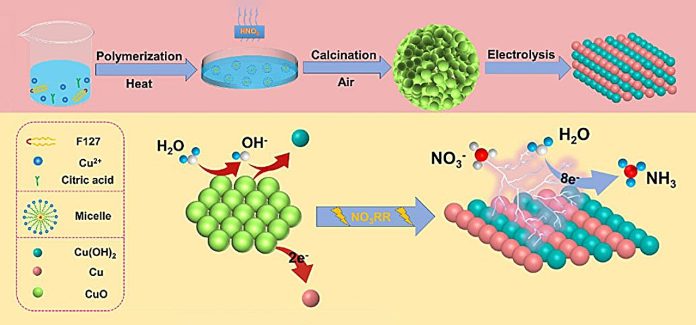
Ammonia is a crucial ingredient in food production and various industries, with a global market of around 175 million metric tons and a value of $67 billion.
It’s also an important player in the emerging hydrogen economy because it can store a lot of energy.
However, the current method for producing ammonia, known as the Haber-Bosch process, is very energy-intensive and generates a large amount of CO2, contributing to climate change.
To address these challenges, a research team led by Hao Li from Tohoku University in Japan has developed a new, more sustainable way to produce ammonia.
Their method focuses on the electrochemical conversion of nitrate (NO3–) to ammonia (NH3), which could revolutionize how ammonia is made while reducing environmental impact.
The details of their work were published in the journal Advanced Science.
Traditionally, ammonia production involves breaking the strong nitrogen bonds in nitrogen gas (N2) through a process called the nitrogen reduction reaction (NRR). This is difficult and energy-consuming.
However, the researchers found that using nitrate (NO3–) as the starting material is much easier and more efficient.
Nitrate has lower energy requirements and dissolves more easily in water, making it a better source for producing ammonia. Additionally, using nitrate can help reduce its accumulation in water systems, which is an environmental problem.
The key to this new process is a specially designed copper-based catalyst. The team created a catalyst made of copper (II) oxide (CuO) particles that are packed together with tiny oxygen-rich gaps.
This catalyst significantly boosts the production of ammonia, achieving a high yield of 15.53 milligrams per hour per milligram of catalyst, with an impressive efficiency of 90.69% in a neutral solution at a voltage of -0.80 V.
One of the most exciting discoveries was that the catalyst changes during the reaction. As the electrochemical process takes place, the CuO catalyst transforms into a new structure made of copper and copper hydroxide (Cu/Cu(OH)2).
This transformation increases the number of active sites where the reaction can occur and improves how electrons move across the catalyst’s surface, making the reaction more efficient.
To better understand how this catalyst works, the researchers used a method called density functional theory (DFT) calculations.
These calculations showed that the Cu(OH)2 structure lowers the energy needed for nitrate to attach to the catalyst, making the process smoother and more efficient.
It also helps prevent unwanted reactions, such as the production of hydrogen gas, and makes it easier for hydrogen atoms to combine with nitrogen to form ammonia.
This research represents a big step forward in designing copper-based catalysts for cleaner ammonia production.
By fine-tuning the reaction conditions and understanding how the catalyst changes during the process, the researchers believe they can further improve the efficiency and stability of this method.
Their ultimate goal is to make ammonia production more sustainable and environmentally friendly, bringing us closer to a greener future.
Source: Tohoku University.