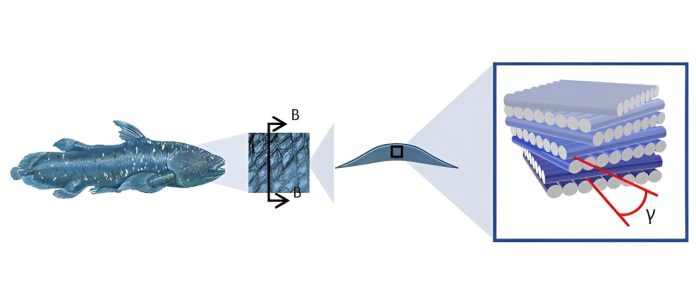
Researchers at Princeton University have developed a groundbreaking method to make concrete stronger and more resistant to cracks, taking inspiration from nature.
This new approach, which uses advanced robotics and 3D printing techniques, could significantly improve the durability of concrete structures like beams and columns.
The study, led by Reza Moini, an assistant professor of civil and environmental engineering at Princeton, was published in the journal Nature Communications.
The team’s innovative design is inspired by the double-helical structure found in the scales of an ancient fish called the coelacanth.
Nature often uses such clever designs to enhance the strength and toughness of materials, and the researchers sought to replicate this in concrete.
By arranging concrete in a specific, layered pattern, they were able to increase its resistance to cracking by up to 63% compared to traditional concrete.
To achieve this, the researchers used a method called robotic additive manufacturing, which is essentially 3D printing for concrete.
In this process, a robot builds structures layer by layer, adding concrete strand by strand. This allows for the creation of complex shapes and internal structures that are not possible with conventional methods like casting.
The key to their success lies in the design of the concrete layers. Instead of stacking the layers in a straightforward manner, the researchers slightly rotated each layer to create a double-helical (or twisted) arrangement.
This double-helix design is crucial for improving the material’s ability to resist cracks. When a crack does form, this design helps to either stop the crack from spreading or redirect it in a way that prevents it from causing significant damage.
Shashank Gupta, a graduate student at Princeton and co-author of the study, explained that using robots is essential for creating these precise designs on a large scale.
Traditional methods of making concrete structures don’t allow for such intricate internal arrangements, which is why the precision and automation provided by robotics are so important.
The robots in Moini’s lab are equipped with advanced processing systems that enable them to create full-sized structural components that are both strong and visually appealing.
One of the challenges the researchers faced was ensuring that the concrete didn’t deform under its own weight during the construction process.
When a robot deposits concrete, the weight of the upper layers can cause the lower layers to shift or deform, compromising the overall structure. To solve this problem, the team developed a customized solution that better controls the rate at which the concrete hardens.
The robotic system they used has two inlets: one for the concrete itself and another for a chemical accelerator. These materials are mixed together just before being extruded by the robot. The accelerator speeds up the hardening process, helping to prevent the concrete from deforming as new layers are added.
By carefully adjusting the amount of accelerator used, the researchers were able to maintain precise control over the shape and structure of the concrete, ensuring it stayed strong and stable.
This innovative approach to concrete design could have far-reaching implications for the construction industry. By making concrete more resistant to cracks, it could lead to longer-lasting and more durable structures, reducing the need for repairs and maintenance. Additionally, the use of robotics and 3D printing opens up new possibilities for creating complex architectural designs that were previously impossible with traditional methods.
Overall, this research marks a significant step forward in the quest to improve the performance and sustainability of concrete, one of the most widely used materials in the world.