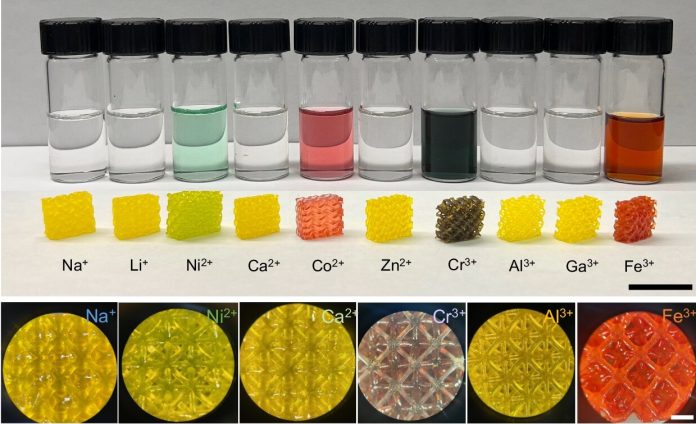
Imagine a material that can change its shape, respond to light, or even act like an artificial muscle—all on demand.
This is the promise of a new type of smart gel, called metallo-polyelectrolyte complexes (MPECs), which scientists have been studying with great interest.
These unique materials, which combine the properties of soft polymers and electrolytes, can be controlled externally using magnetic, electrochemical, or optical signals.
This makes them ideal for a wide range of applications, including energy devices, responsive actuators, and nanofiltration systems.
MPECs are made of metal ions that form dynamic, reversible ionic bonds with polymer chains. Unlike covalent bonds, which are very strong and difficult to break, these ionic bonds can be easily rearranged, allowing the material to change its properties when stimulated.
While researchers have known about these materials and their unusual properties for some time, the exact reasons behind their behavior remained a mystery. Moreover, previous methods for making MPECs were not easy to scale up and often resulted in uneven material composition.
Now, a team of scientists from Caltech has developed a comprehensive framework for understanding and designing MPECs.
Their work, published in the journal Nature Communications, provides a “roadmap” for creating gels with specific properties, from the molecular level all the way up to the full material scale.
“Our lab usually focuses on materials that respond to external stimuli because of their specific micro- or nano-architectures,” explains Julia R. Greer, a leading researcher on the project and a professor at Caltech. “What’s exciting about MPECs is that they can be activated without needing such complex structures.”
These materials can exhibit a wide range of properties depending on the metal ions used and the pH level during their formation. For example, one sample could be designed to bend in different directions depending on how fast a force is applied to it. In another case, a gel might dissolve completely in water or remain solid for days, with the difference being the type of metal ion involved.
This flexibility opens up new possibilities for designing materials that can adapt to their environment. Such materials could be used in technologies that were previously challenging to develop, like self-monitoring filters, advanced membranes for ion exchange, and even artificial muscles.
The key to this changeability lies in the metal ions at the core of MPECs and their interactions with charged polymer chains. Many transition metals are multivalent, meaning they can have more than one charge state. For example, iron can exist as Fe2+, which typically binds to two polymer chains, or Fe3+, which binds to three chains. By adjusting the metal’s charge state, scientists can “tune” the properties of the gel.
To better understand these interactions, the Caltech team used a combination of laboratory experiments, computational modeling, and advanced manufacturing techniques like stereolithography—a type of 3D printing. This allowed them to create solid structures layer by layer using a light-induced polymerization process. By incorporating different metal ions into the resin used for printing, they were able to produce a stable polymer with metal ions bound to it.
The researchers then conducted a series of thermal and mechanical tests on the materials to see how they responded at different scales. Pierre Walker, a co-lead author of the study and a graduate student in chemical engineering at Caltech, analyzed the data and created models to explain how the materials behave from the molecular level up to the full material scale.
“A lot of this investigation felt like walking around in the dark,” Walker admits. “But by coupling different effects—like the metal ion’s charge state, pH levels, and the solvent used—we were able to understand how they interact and affect the material’s overall properties.”
In their paper, the researchers describe several examples of MPECs they designed using their new framework. In one case, they created a shape-memory polymer that could “remember” its original shape after being deformed. For this experiment, they made a yellow gummy flower that lay flat at room temperature. When heated to 90°C, the petals were manually folded into a bud. After cooling to -5°C and reheating, the flower returned to its original flat shape. The speed and completeness of this transformation depended on the type of metal ion used.
In another example, the scientists created a gel strip with different pH levels on each side. When submerged in water, the strip buckled in one direction; when placed in an aluminum solution, it buckled in the opposite direction. This behavior matched the theoretical predictions made by the researchers.
“We now have a solid explanation for how small molecular changes can lead to big differences in the material’s properties,” says Seneca Velling, a former graduate student in the Greer group. “This means we can design materials from the ground up or explain their behavior from the top down.”
The team’s work provides a powerful tool for future researchers and engineers, allowing them to design smart materials with unprecedented control and precision. With this new understanding, the possibilities for MPECs are vast, potentially leading to innovations in areas like healthcare, energy, and environmental protection.