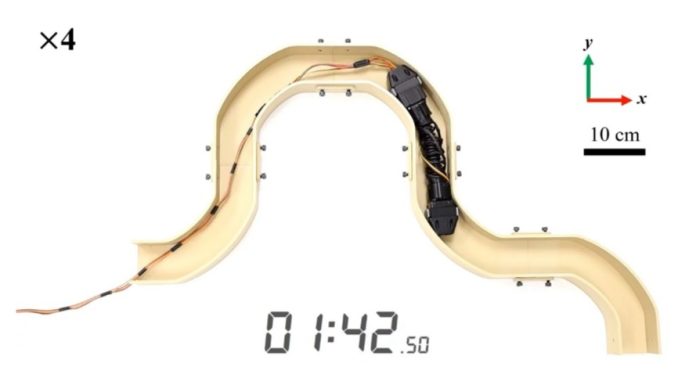
Northwestern engineers have created a new soft, flexible device that makes robots move by expanding and contracting, similar to how human muscles work.
To show off their new invention, called an actuator, the researchers built a worm-like soft robot and an artificial bicep.
In tests, the worm-like robot successfully navigated the twists and turns of a narrow pipe, while the artificial bicep could lift a 500-gram weight 5,000 times without breaking.
The soft actuator’s body was 3D-printed using common rubber, making the robots cost around $3 in materials, excluding the small motor needed to change the actuator’s shape.
This is much cheaper compared to traditional stiff, rigid actuators used in robotics, which can cost hundreds or even thousands of dollars.
Researchers believe this new actuator could lead to the development of affordable, soft, flexible robots that are safer and more practical for everyday use.
Ryan Truby, a leading researcher at Northwestern, explained that soft robots are less likely to cause injury if they hit a person compared to hard, rigid robots.
These inexpensive actuators could be used to create robots better suited for human environments.
Truby, who directs The Robotic Matter Lab at Northwestern, led the study with Taekyoung Kim, a postdoctoral scholar, and Pranav Kaarthik, a Ph.D. candidate in mechanical engineering.
Traditionally, robots have used rigid actuators, but these lack flexibility, adaptability, and safety. This has pushed researchers to explore soft actuators.
Truby and his team aimed to make materials that move like human muscles, which both contract and stiffen at the same time.
To develop their actuator, the team 3D-printed structures called “handed shearing auxetics” (HSAs), which can extend and expand when twisted. In the past, similar structures were printed using expensive printers and rigid plastic.
This time, they used thermoplastic polyurethane, a common, inexpensive rubber, making the HSAs softer and more flexible. They also used a standard desktop 3D printer.
Earlier HSA soft actuators required multiple motors to twist the materials, making the design complex and less soft. The team aimed to create a single HSA driven by one motor. Kim added a rubber bellows to the structure, acting like a flexible, rotating shaft. As the motor turned, the actuator extended or contracted like a muscle.
This simplified design allowed Kim to build a crawling robot from a single actuator, moving through a winding environment by pushing and pulling itself forward.
“Our robot can move using a single structure,” Kim said. “This makes our actuator more versatile and easier to integrate into various robotic systems.”
The resulting robot was compact (26 centimeters long) and could crawl at a speed of 32 centimeters per minute. An interesting feature is that both the robot and artificial bicep become stiffer when fully extended, similar to human muscles when doing work.
“Many soft actuators get softer when in use, but ours get stiffer,” Truby explained. “This muscle-like stiffening is important for performing tasks that require force.”
Truby and Kim believe their new actuator is a step closer to creating robots that move like living organisms, opening up possibilities for robots to perform tasks conventional robots can’t.