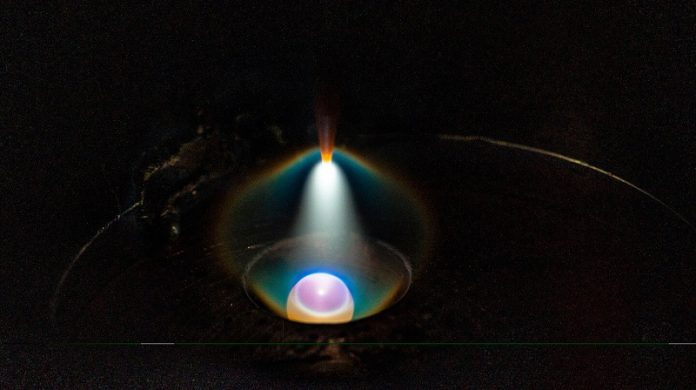
At around 2,500 degrees Fahrenheit, steel melts. When aluminum is exposed to moisture and oxygen, it corrodes.
While these metals are great for everyday use, they can’t handle extreme conditions like intense heat, cold, or pressure.
As the nation increasingly operates in extreme environments, such as space and the Arctic, there’s a critical need for stronger alloys that can withstand these conditions.
Multi-principal element alloys (MPEAs) are made from several elements in nearly equal amounts.
These alloys are better suited for extreme environments because they are very strong, hard, and tough at various temperatures.
MPEAs also resist corrosion well and remain stable under high heat. Additionally, they can have unique properties useful for electronic or magnetic devices.
Researchers at the Johns Hopkins Applied Physics Laboratory (APL) in Laurel, Maryland, are speeding up the design of MPEAs by creating complex microstructures from a few samples that provide a lot of data.
This new approach helps them link the different phases of an alloy—distinct materials formed when an alloy is heated or cooled—to their mechanical properties.
In a study published in the journal Data in Brief, the researchers described how they used this new method to create 17 unique MPEA compositions.
“Designing MPEAs is challenging because even small changes in composition can lead to large changes in material properties,” said Morgan Trexler, a program manager at APL.
Their new technique allows researchers to quickly create and analyze thousands of local data points within bulk samples. This speeds up the discovery of new materials. To predict which MPEA compositions to make, APL partnered with Paulette Clancy and Maitreyee Sharma Priyadarshini at the Johns Hopkins Whiting School of Engineering.
With limited data, Clancy and Sharma Priyadarshini used their algorithm, PAL 2.0, to quickly sort through alloy possibilities and suggest MPEAs that would be very hard and provide a wide range of data for future development.
Unlike most deep-learning efforts that require large databases, their algorithm needed only about a dozen data points to make useful recommendations.
“We created a closed-loop cycle,” Clancy explained. “We run APL’s data through PAL 2.0 to make predictions of compositions. APL makes and tests the suggested alloys, analyzes the results, and then we restart the process with the new data. We’re constantly improving our results.”
The team keeps building on each test’s results. In the first round, the algorithm recommended alloy possibilities that were too expensive or couldn’t be manufactured. They are now in their third cycle, which is identifying alloys more than twice as hard as before.
After Clancy’s group suggests which alloys to test, the APL team creates the alloys and melts them using an electric current. This arc melting method uses minimal material, allowing them to quickly sample different compositions.
“When the alloy is melted, it creates dozens of different materials with different chemical compositions within one sample,” said Eddie Gienger, a materials scientist at APL and lead author of the study.
The team uses scanning electron microscopy (SEM) and energy-dispersive X-ray spectroscopy (EDS) to measure phase compositions, and nanoindentation to measure hardness.
“With nanoindentation, we can automatically collect measurements from hundreds of locations on the sample and map those to phase compositions to understand how each microstructure and composition behaves,” added Lisa Pogue, a materials scientist at APL.
This approach helps identify new, potentially useful materials. By coupling this with mechanical property information, they can find promising compositions for future alloy development. The data, which included 17 unique MPEA compositions and over 7,000 data points, was compiled into a database for future use.
“The process helps identify the potential of MPEAs,” Gienger said. “If a material needs specific mechanical properties like hardness, this method provides the information needed to design those properties.”
APL is developing and testing many techniques to speed up material discovery and understanding. “The more tools we have for high-throughput characterization, the more opportunities we have to apply them in areas needing new, stronger materials,” Trexler said.
This new pathway to stronger alloys could lead to better materials for extreme environments, ensuring that operations in space, the Arctic, and other harsh conditions are successful and safe.
Source: Johns Hopkins University.