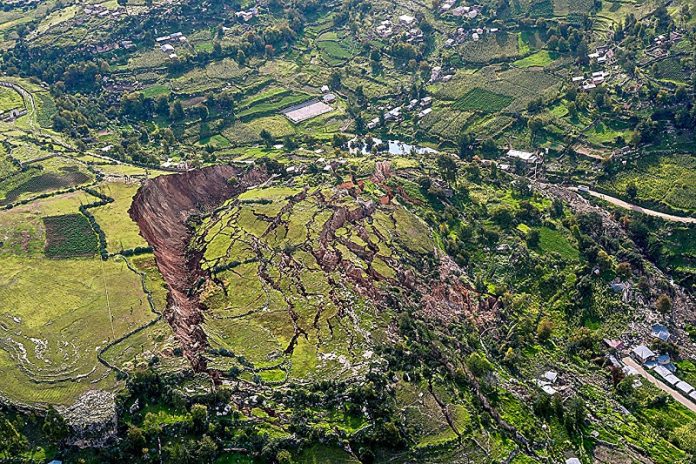
Understanding how soft materials break under stress is crucial for solving various engineering problems, from pharmaceutical technology to preventing landslides.
A recent study has introduced a new parameter called the “brittility factor” that links a range of soft material behaviors previously thought to be unrelated.
This discovery can help engineers design better materials for future challenges.
The research, published in the journal Proceedings of the National Academy of Sciences, was led by Professor Simon Rogers and graduate student Krutarth Kamani from the University of Illinois Urbana-Champaign.
Their work focuses on how soft materials respond to stress, showing that solid and liquid states can exist together in these materials.
This field is essential for industrial, environmental, and biomedical applications.
The team found that there was a communication gap among scientists studying soft materials, which created a bottleneck between theoretical understanding and practical applications.
Soft materials, whether natural or synthetic, deform under pressure until they reach a point where they either return to their original shape or undergo permanent deformation.
This process is known as yielding. Gradual yielding is termed ductile behavior, while abrupt yielding is referred to as brittle behavior.
“At a recent conference, we realized that all of us who study soft materials from Europe and North America couldn’t agree on the connection between brittle and ductile behavior nor how to define it,” Rogers said.
Instead of viewing soft material behavior as either brittle or ductile, Rogers’s team considered a spectrum of yielding behaviors. This approach led them to develop a continuum model and identify the brittility factor.
This factor is crucial in determining how and why soft materials fail.
Essentially, the brittility factor influences how a material deforms permanently under stress. The model suggests that the higher the brittility factor, the less a soft material will deform permanently before yielding.
The model was developed and tested using data from numerous experiments that subjected various soft materials to stress. The individual strain responses were measured using a device called a rheometer.
“We didn’t expect this study to explain as much as it does,” said Rogers, who is also affiliated with the Beckman Institute for Advanced Science and Technology.
“We ended up with a way to bring together a whole range of soft material behaviors under the same physics umbrella. Previously, these behaviors were studied independently or applied simultaneously without being physically or mathematically connected.”
This finding will allow researchers to explain why some materials are more resistant to rapid yielding than others, a question that has puzzled scientists for decades.
“This single parameter amazingly connects so many puzzling observations researchers have come across over the years,” Kamani said.
“This work marks the point at which we are approaching the crest of the hill in understanding soft materials behavior,” Rogers added. “We’ve always felt like each step takes us higher, but with no end in sight. Now we can see the top of the hill and are free to move forward in whatever direction we would like.”
This breakthrough will enable more precise and efficient design of soft materials, leading to advancements in various fields.