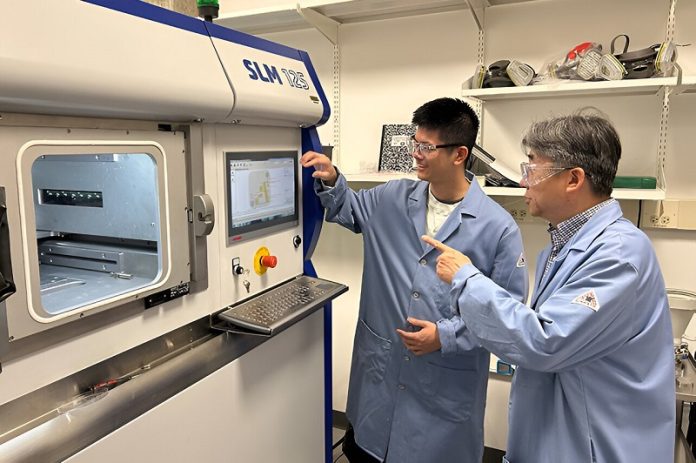
Researchers at Purdue University have invented a new way to create ultra-strong aluminum alloys that can be used in 3D printing.
This breakthrough, developed by engineers Haiyan Wang and Xinghang Zhang, along with graduate student Anyu Shang, promises to enhance industries like aerospace and automobile manufacturing, where lightweight and high-strength materials are crucial.
Traditional high-strength aluminum alloys have limitations when it comes to 3D printing because they are prone to a problem called hot cracking.
This issue creates defects in the metal, leading to weakened structures.
To address this, the Purdue team introduced transition metals—cobalt, iron, nickel, and titanium—into aluminum. These metals were formed into nanoscale, laminated structures that prevent cracking and increase strength.
“Our work shows that the proper introduction of heterogenous microstructures and nanoscale medium-entropy intermetallics offers an alternative solution to design ultra-strong, deformable aluminum alloys via additive manufacturing,” Zhang explained.
“These alloys improve upon traditional ones that are either ultra-strong or highly deformable, but not both.”
The researchers have applied for a patent to protect their innovation, which was published in the journal Nature Communications.
Lightweight, high-strength aluminum alloys are essential for many industries. However, most of these alloys can’t be used in 3D printing because they crack under the heat, creating defects.
Traditional methods to strengthen aluminum alloys involve adding particles to impede dislocation movements, but even the best alloys produced this way only reach strengths of 300 to 500 megapascals, much lower than the 600 to 1,000 megapascals achievable by steels.
The new method by the Purdue researchers incorporates transition metals into the aluminum, forming them into nanoscale, intermetallic layers. These layers are organized into fine rosette shapes that reduce brittleness and enhance strength.
The Purdue team conducted various tests to ensure the effectiveness of their new aluminum alloys. These tests included macroscale compression tests, micropillar compression tests, and post-deformation analysis.
The results showed that the new alloys combined high strength, exceeding 900 megapascals, with significant plastic deformability. In some areas, the alloys demonstrated flow stresses over a gigapascal.
Haiyan Wang highlighted that the new method leverages laser-based additive manufacturing to rapidly melt and cool the materials, introducing the nanoscale intermetallic layers that are key to the alloy’s strength and flexibility.
This process creates heterogeneous microstructures that improve the material’s ability to harden under stress.
The successful development of these new aluminum alloys opens up exciting possibilities for their use in 3D printing, potentially revolutionizing the production of high-strength, lightweight components in various industries.
This innovation represents a significant step forward in materials engineering, combining the best properties of strength and deformability in a single alloy suitable for advanced manufacturing techniques.