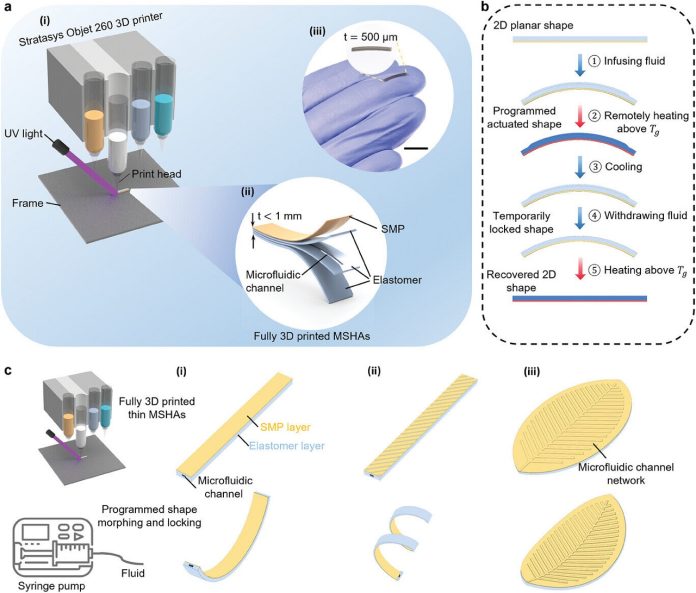
Researchers at North Carolina State University have created tiny hydraulic devices, called actuators, that can control the movement and shape of soft robots less than a millimeter thick.
These mini actuators use a new method that combines 3D printing with special materials to allow the robots to lock into different shapes and return to their original form when needed.
“Soft robotics is promising for many applications, but designing the actuators that drive their movement on a small scale is challenging,” says Jie Yin, the lead author of the study and an associate professor at NC State.
The team’s approach uses multi-material 3D printing technologies and shape memory polymers to create these soft actuators on a very small scale, providing exceptional control and precision.
The technique involves making soft robots with two layers. The first layer is a flexible polymer with a pattern of tiny channels, made using 3D printing.
The second layer is a flexible shape memory polymer. The combined soft robot is just 0.8 millimeters thick.
By pumping fluid into the channels, hydraulic pressure is created, causing the soft robot to move and change shape.
The pattern of the channels determines how the robot moves—whether it bends, twists, or performs other actions. The amount and speed of fluid introduced control how fast the robot moves and the force it exerts.
To “freeze” the soft robot in a particular shape, moderate heat (64°C, or 147°F) is applied, and then the robot is allowed to cool briefly. This locks the robot into its new shape even after the fluid is removed.
To return the robot to its original shape, heat is applied again after the fluid is pumped out, allowing the robot to relax back.
“A key factor here is fine-tuning the thickness of the shape memory layer relative to the layer with the channels,” explains Yinding Chi, co-lead author and a former Ph.D. student at NC State. “The shape memory layer must be thin enough to bend when pressure is applied, but thick enough to retain the shape once the pressure is removed.”
To demonstrate this technology, the researchers created a soft robot “gripper” capable of picking up small objects.
By applying hydraulic pressure, the gripper closed on an object. Then, by applying heat, they fixed the gripper in its closed position, even after the pressure was released.
The gripper could then be moved to a new location, carrying the object with it. When heat was applied again, the gripper released the object.
This innovative technology shows great potential for controlling the movement and shape of tiny soft robots, opening up new possibilities in fields like medicine and manufacturing.
Source: North Carolina State University.