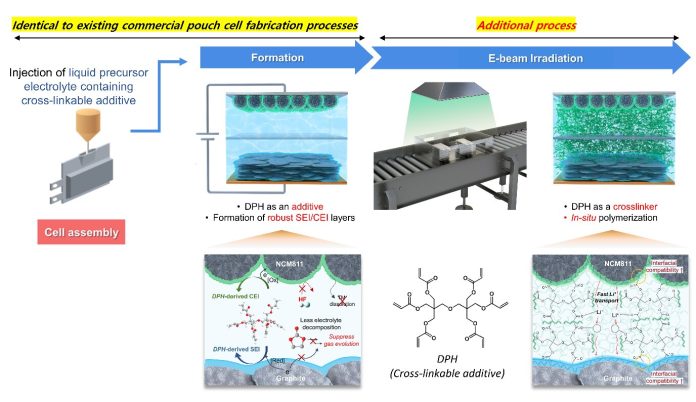
Researchers at Pohang University of Science and Technology (POSTECH) in South Korea have made a significant breakthrough in battery technology.
Led by Professor Soojin Park, Ph.D. candidate Seoha Nam, and Dr. Hye Bin Son, the team has developed a gel electrolyte that makes lithium-ion batteries safer and more commercially viable.
Their findings were published in the journal Small.
Lithium-ion batteries are commonly used in everything from smartphones to electric vehicles because they can store a lot of energy in a small space.
However, the liquid electrolytes used in these batteries can catch fire or explode, posing a significant safety risk. This has led scientists to search for safer alternatives.
The gel electrolyte solution
One promising alternative is the semi-solid-state battery, which uses a gel-like substance instead of a liquid.
This type of battery offers better stability and can store more energy, potentially lasting longer than traditional lithium-ion batteries. However, making these gel electrolytes has been challenging.
The process usually involves heating the materials to high temperatures, which can damage the electrolyte and increase production costs.
There’s also the issue of high resistance at the interface between the electrolyte and the electrodes, which reduces the battery’s performance.
Professor Park’s team addressed these challenges using a new method. They introduced a special additive called dipentaerythritol hexaacrylate (DPH) and used electron beam (e-beam) technology.
Normally, making a pouch-type battery involves several steps: preparing the electrodes, injecting the electrolyte, assembling the parts, activating the battery, and removing any excess gases. The researchers added an extra step after degassing, where they exposed the battery to e-beam irradiation.
This helped the DPH additive to form a stable structure and create a strong bond between the anode and cathode surfaces.
The new gel electrolyte significantly reduced the gas generated during the battery’s initial charge and discharge cycles, cutting it down by 2.5 times compared to traditional batteries. This reduction in gas generation is crucial because it prevents the battery from swelling and losing capacity.
The researchers tested their new battery design by creating a high-capacity battery with 1.2 ampere-hours (Ah) and evaluated its performance at 55 degrees Celsius, a temperature that usually speeds up electrolyte breakdown.
Conventional batteries with liquid electrolytes generated a lot of gas and lost capacity quickly, swelling up after just 50 cycles.
In contrast, the new gel electrolyte battery showed no gas generation and maintained a capacity of 1 Ah even after 200 cycles. This demonstrates that the new battery is both safer and more durable.
One of the most exciting aspects of this research is its potential for mass production.
The new gel electrolyte can be integrated into existing pouch battery production lines with just one additional step. This makes it easier and more cost-effective to produce safer batteries on a large scale.
Professor Soojin Park highlighted the significance of this breakthrough, especially for the electric vehicle industry.
Safer, more reliable batteries could greatly benefit electric vehicles and many other applications that rely on lithium-ion batteries.
This advancement in battery technology could lead to longer-lasting, more efficient, and safer batteries, helping to power the future of sustainable transportation and beyond.
In summary, the development of this new gel electrolyte by POSTECH researchers represents a major step forward in making lithium-ion batteries safer and more commercially viable, paving the way for broader adoption in various industries.
Source: KSR.