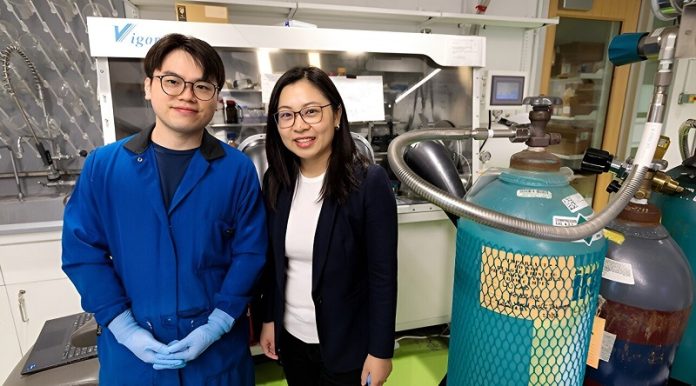
As the demand for electric vehicles rises, so does the need for lithium, a crucial component in lithium-ion batteries.
However, current methods for extracting lithium from rock ores or brines are slow, energy-intensive, and harmful to the environment.
These methods also rely on highly concentrated lithium sources found in only a few countries.
Researchers at the University of Chicago’s Pritzker School of Molecular Engineering (PME) have now optimized a new method for extracting lithium from more dilute sources, such as seawater, groundwater, and “flowback water” from fracking and offshore oil drilling.
This breakthrough, led by Chong Liu, Neubauer Family Assistant Professor of Molecular Engineering, was published in Nature Communications.
“There’s a gap between the demand for lithium and its production,” said Liu. “Our method allows efficient extraction from very dilute liquids, which can greatly expand the potential sources of lithium.”
In this research, Liu and her team demonstrated how iron phosphate particles can efficiently pull lithium out of these dilute liquids. This finding could lead to faster and greener lithium extraction.
The environmental cost of lithium extraction
Most lithium today comes from two extraction methods. The first involves mining lithium rock ores, crushing them with heavy machinery, and treating them with acid to isolate the lithium.
The second method uses lithium brine pools, where massive amounts of water are pumped to the surface and evaporated over more than a year to yield dried lithium.
“These methods aren’t environmentally friendly, and they become even less efficient with less concentrated sources of lithium,” said Liu. “If you have a brine that’s 10 times more dilute, you need 10 times more water to get the same amount of lithium.”
Liu’s team has pioneered a different method to extract lithium from dilute liquids. Their approach uses the electrochemical properties of crystal lattices of olivine iron phosphate.
Lithium, due to its size, charge, and reactivity, is drawn into the spaces in these iron phosphate columns, similar to water being absorbed by a sponge. Properly designed, these columns exclude sodium ions, which are also present in briny liquids.
In the new study, Liu and her colleagues, including first author Gangbin Yan, a PME graduate student, tested how variations in olivine iron phosphate particles affected their ability to selectively isolate lithium over sodium.
Finding the optimal particle size
The research team synthesized olivine iron phosphate particles using different methods, creating a range of particle sizes from 20 to 6,000 nanometers. They then grouped these particles by size and used them to build electrodes to extract lithium from a weak solution.
They discovered that particles too large or too small allowed more sodium into their structures, leading to less pure lithium extractions. “There was a sweet spot where both the kinetics and thermodynamics favored lithium over sodium,” Liu explained.
These findings are crucial for moving electrochemical lithium extraction toward commercial use. The researchers now know that producing olivine iron phosphate at the ideal particle size is essential.
“We need to keep this desired particle size in mind as we scale up our synthesis methods,” said Liu. “If we can do this, we believe we can develop a method that reduces the environmental impact of lithium production and secures the lithium supply in this country.”
This new method holds promise for a more sustainable future, where lithium can be efficiently and responsibly extracted from widely available, dilute sources.
Source: University of Chicago.