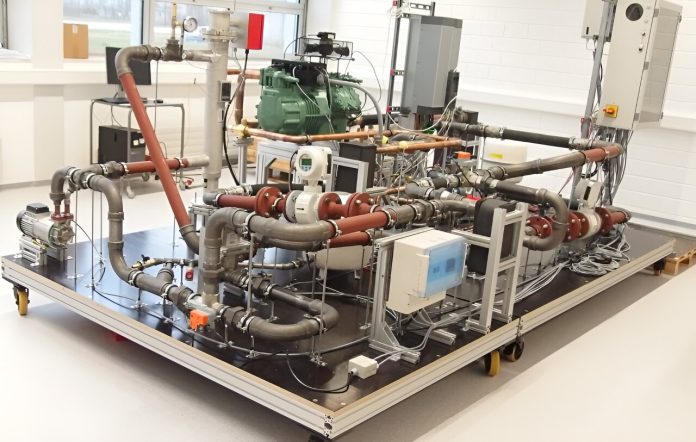
Industrial companies need process heat for many applications, from producing food and beverages to making metals and paper.
Traditionally, this heat is generated by burning fossil fuels, which contributes significantly to greenhouse gas (GHG) emissions.
In Switzerland, industrial process heat is responsible for about 8% of total GHG emissions.
Currently, industrial heat pumps can generate heat up to 200 degrees Celsius using electricity from renewable sources, offering a more eco-friendly solution.
However, these heat pumps are not widely used in industrial settings because they are expensive and custom-made for specific applications.
Researchers from ETH Zurich and the Eastern Switzerland University of Applied Sciences in Buchs have developed a more flexible and cost-effective solution.
Their new heat pump technology can generate heat at various temperatures up to 200 degrees Celsius, making it suitable for a wide range of industrial needs. This innovation has already attracted interest from several Swiss and international companies.
The study detailing this breakthrough was published in the International Journal of Refrigeration.
How heat pumps work
Heat pumps capture energy from waste heat or the environment (like air, groundwater, or soil).
They operate by evaporating a refrigerant fluid in a closed system and then compressing the gas to increase its temperature. The heat produced can be used for heating buildings or industrial processes.
In conventional heat pumps, the choice of refrigerant largely determines the achievable temperature. All the components of the heat pump—evaporator, compressor, condenser, and expansion valve—are designed around this specific refrigerant. If a factory needs heat at different temperatures, it would require multiple heat pumps with different refrigerants, which is both costly and impractical.
A flexible solution with refrigerant blends
André Bardow, a professor at ETH Zurich, and his team have devised a better solution: using a blend of refrigerants instead of a single one.
This allows a single heat pump to handle different heat sources and generate various temperature profiles. By changing the composition of the refrigerant blend, the heat pump can be easily adapted to different applications, making it much more flexible and cost-effective.
The refrigerant blend consists of a traditional refrigerant and an additional component. The temperature profile of the heat pump is determined by the ratio of these two ingredients.
“In principle, you can have any number of different profiles for industrial processes, as long as the temperatures don’t exceed 200 degrees. That’s the major advantage our technology offers,” says Bardow.
Using computer models to optimize the blend
To identify the best components for the refrigerant blend, the researchers developed a computer model that simulates the heat-pump circuit with different mixtures.
Dennis Roskosch, a senior scientist in Bardow’s group, explains, “We extended existing thermodynamic models for heat pumps by integrating the heat-pump components and the composition of the mixture into the optimization process.”
The model uses over 200 million known synthetic molecules to simulate blends that offer the most efficient heat-pump performance. This innovative approach allows the researchers to pinpoint the best refrigerant mixture for any given industrial application.
This new heat pump technology has the potential to significantly reduce GHG emissions from the industrial sector by providing a flexible and eco-friendly alternative to fossil fuel-based heating. It represents a major step forward in the quest for sustainable industrial processes.