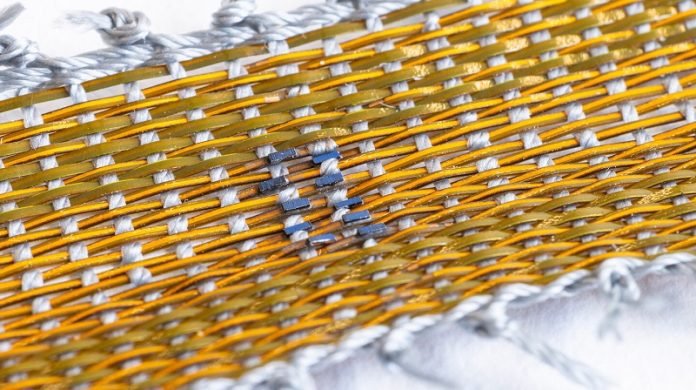
Researchers at Johns Hopkins Applied Physics Laboratory (APL) in Maryland have developed new methods to create battery- and solar-powered fibers. This breakthrough could make it possible to harvest and store electrical energy directly in the clothes we wear.
These innovative fibers could power wearable electronics that breathe, stretch, and wash just like regular clothing.
Imagine a shirt with built-in power that can monitor your heart, keep you warm, or help soldiers record audio and video hands-free.
“As demands for electronic textiles change, there is a need for smaller power sources that are reusable, durable, and stretchable,” said Konstantinos Gerasopoulos, lead investigator of the project.
The new fibers are submillimeter-thin strands that can be woven directly into fabrics. This opens up many possibilities for wearable electronics and smart textiles.
In the past, making fiber batteries has been difficult. Traditional manufacturing methods limited their scalability and performance. Industrial textile equipment could make fiber batteries, but this process was only possible in specialized facilities and wasn’t compatible with the battery industry.
Standard fiber batteries also didn’t perform well because the electrodes were twisted together, leaving most of the surface inactive.
Now, in a study published in Advanced Materials Technologies, APL scientists have found a way to scale up fiber battery production. Instead of using textile equipment, they customized battery equipment to make the fibers thin enough.
This process, using customized roll-to-roll setups, is portable and suitable for large-scale production. All the necessary equipment could fit in a small room.
“We were always designing with roll-to-roll compatibility in mind,” said Rachel Altmaier, the lead author. “We need to be able to run all of our processes continuously, or else what we develop isn’t relevant. This process could be dropped into an existing manufacturing line.”
The batteries are made from flat strips of anode and cathode electrodes and a polymer separator, which are fed into a heated roll press and laminated into a stacked design. The stack is then laser-cut into fiber-like strands about 700 micrometers wide—roughly the width of five human hairs. This is the first use of laser cutting on a full battery stack, proving it can customize battery size and maintain performance.
APL researchers have also developed a flexible lithium-ion battery that works under extreme conditions and safe, fast-charging batteries. In another study published in Advanced Functional Materials, they created high-performing fibers that can harvest light and convert it into electricity.
“Just like with the battery fibers, we were inspired by conventional solar cell technology that is very efficient and robust,” said Gerasopoulos. “We asked, how can we turn these power sources into fibers?”
The team made tiny solar cells on thin, flexible circuit boards and sealed them in a protective polymer to create fiber-like strands. These solar cells are so small they could fit between the ridges of a fingerprint. Even after bending the fiber 8,000 times, its performance remained unchanged.
In a proof of concept, the researchers used a mini loom to weave nylon and solar cell fibers into a small textile. This fabric, placed under a lamp, powered a small LED blinker.
These fibers could also incorporate sensors, LEDs, or other devices, adding various functionalities to the fabric.
“Textiles that integrate light energy harvesting and battery fibers could revolutionize what wearables today can achieve,” said Jeff Maranchi, research program area manager at APL. “Very soon, these fibers will enable distributed fabric-based power, heating, communications, and sensing while providing the comfort and ease of regular textiles.”
Source: Johns Hopkins University.