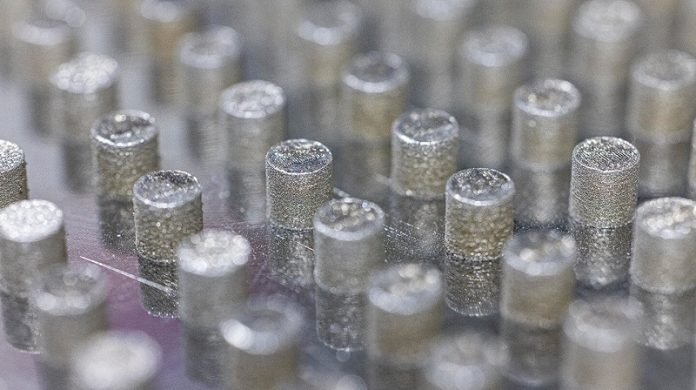
The United States is gearing up for a big boost in manufacturing, thanks to new federal investments aimed at improving production technologies.
This effort includes enhancing additive manufacturing, also known as 3D printing, which builds objects layer by layer.
Additive manufacturing is especially useful because it can create complex and customized shapes for various applications, including national defense, biotechnology, and aerospace.
However, a major challenge with this technology is the formation of defects during printing, which can weaken or break the parts.
Researchers at the Johns Hopkins Applied Physics Laboratory (APL) in Maryland are tackling this issue.
They are developing advanced sensors capable of catching these defects in the early stages, before the parts even finish printing.
The problem often arises during a process called powder bed fusion. Here, lasers melt metal powders to form solid metal shapes.
If the lasers heat the metal too quickly, tiny vapor bubbles can form and get trapped inside, creating weak spots known as keyhole defects.
These defects are tricky to detect because they form underneath the surface of the freshly printed layers.
The APL team, led by experts like Vince Pagán and Steve Storck, is using insights from space technology to address this.
They draw an analogy to how scientists can spot underwater rocks in rivers from space by observing the disruption in water flow. Similarly, by detecting changes in temperature and light during the printing process, the sensors can identify when and where a defect might be forming.
The team’s challenge was to develop a sensor that could react incredibly quickly—within nanoseconds—to adjust the printing process in real time and prevent these defects.
To do this, they collaborated with Mark Foster from Johns Hopkins University and created a high-speed sensor that collects detailed data on the melting process at very high speeds.
This sensor, combined with a high-speed computing device, allows the printer to pause the laser momentarily to let the metal cool just enough to avoid forming a defect. Impressively, their system can respond in less than one microsecond—that’s faster than a blink of an eye!
Their next step is to integrate artificial intelligence into the system. This will help predict and control the printing process more accurately, ensuring that every part is strong and reliable right out of the printer.
This breakthrough in additive manufacturing could lead to safer, more reliable components for critical applications, marking a significant step forward in manufacturing technology.